GUIDE : Rebuilding the rear end
Posted
Settled In

GUIDE : Rebuilding the rear end
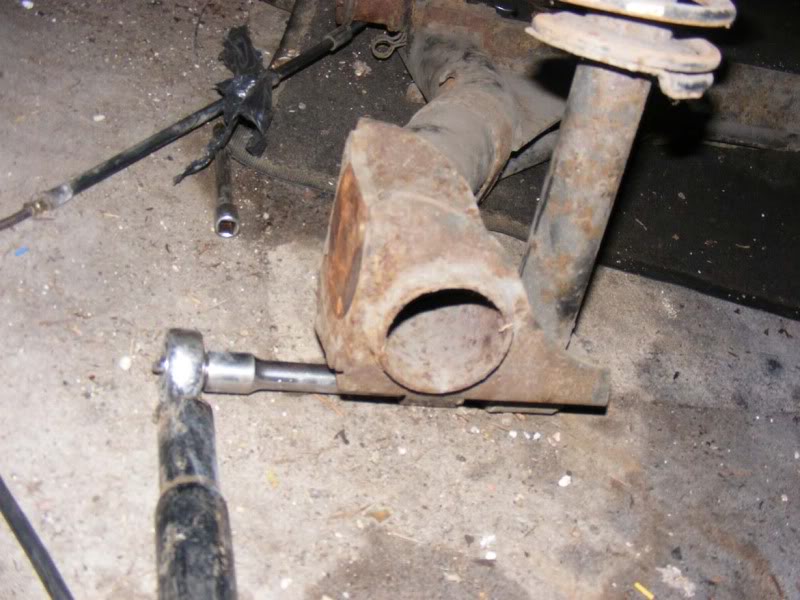
Step 61 - Then you'll need a socket on the nut. If it's rusty and dirty then tap the socket on with a hammer to get a snug fit
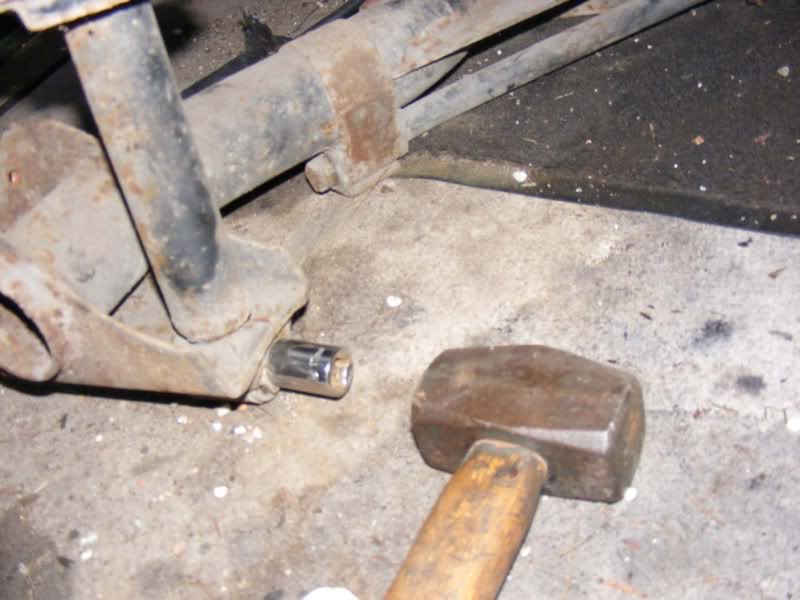
Step 62 - Then put your ratchet on (picture 1) and extend with a bar - I used the end of the jack handle (picture 2)
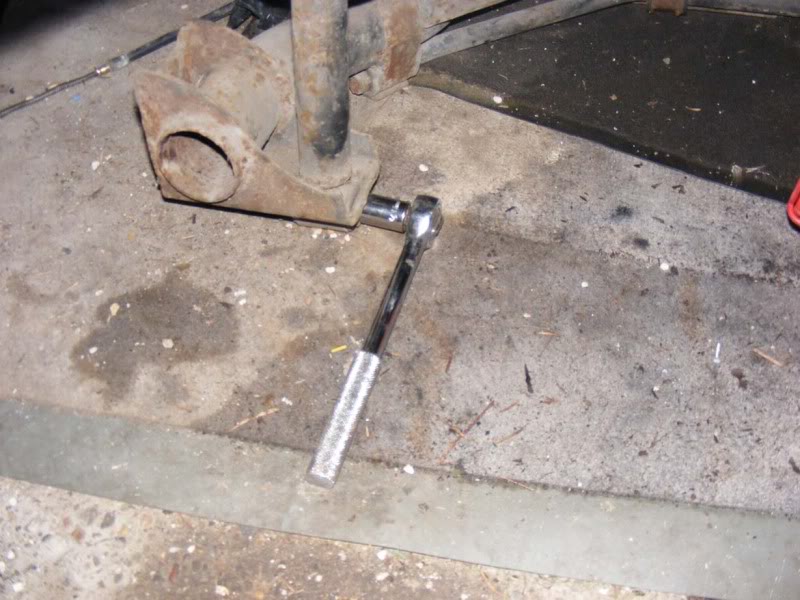
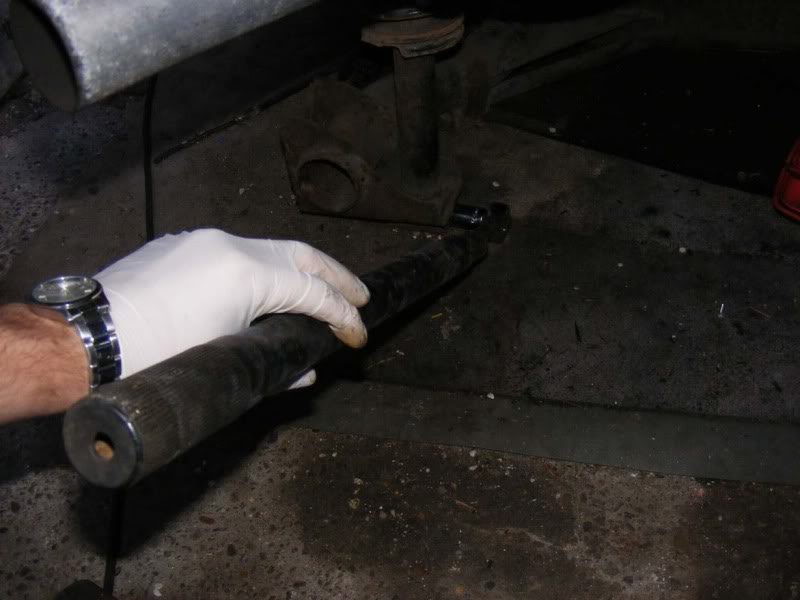
Posted
Settled In

Step 64 - Once removed, tap the end of the bolt back through the strut (you might find rotating the bolt with the 17mm socket you fitted in step 60 helps to free it)
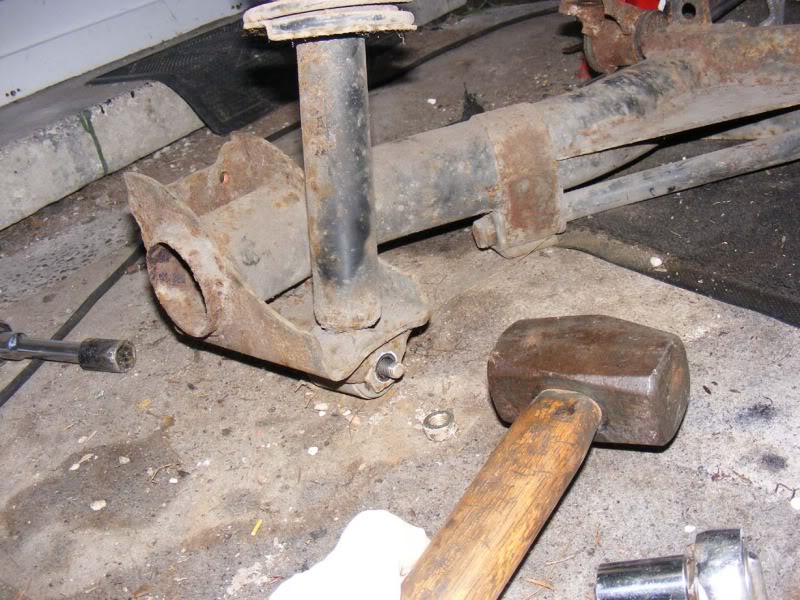
Step 65 - Complete extraction using a screwdriver and the hammer to tap the bolt right out
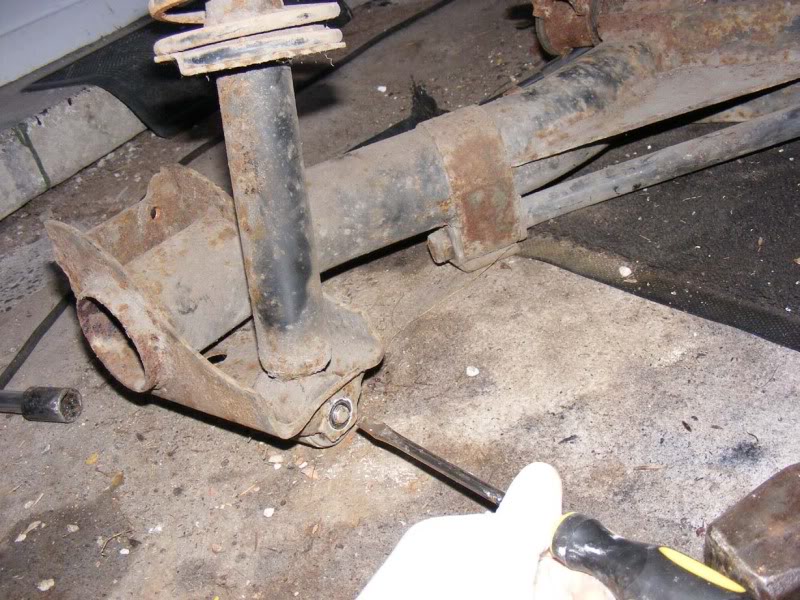
Step 66 - Now you can remove the coil and shock absorber/damper/strut completely
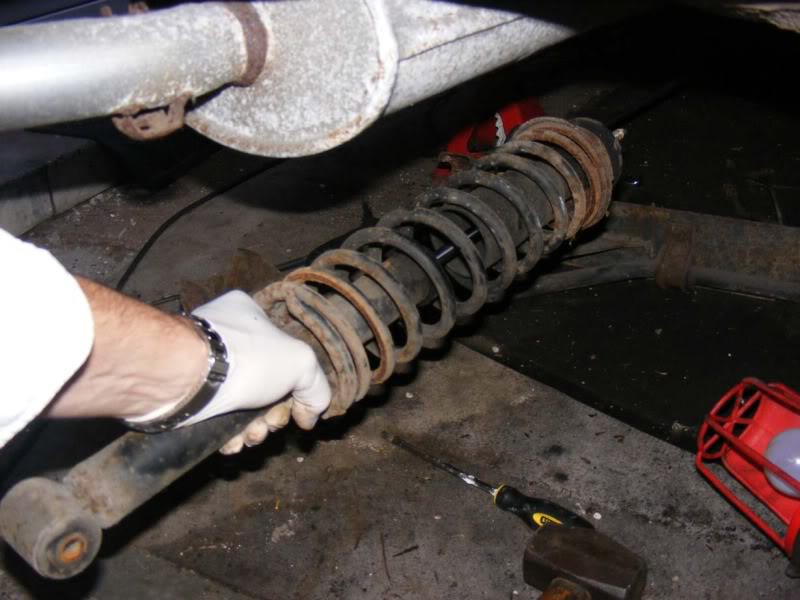
Posted
Settled In

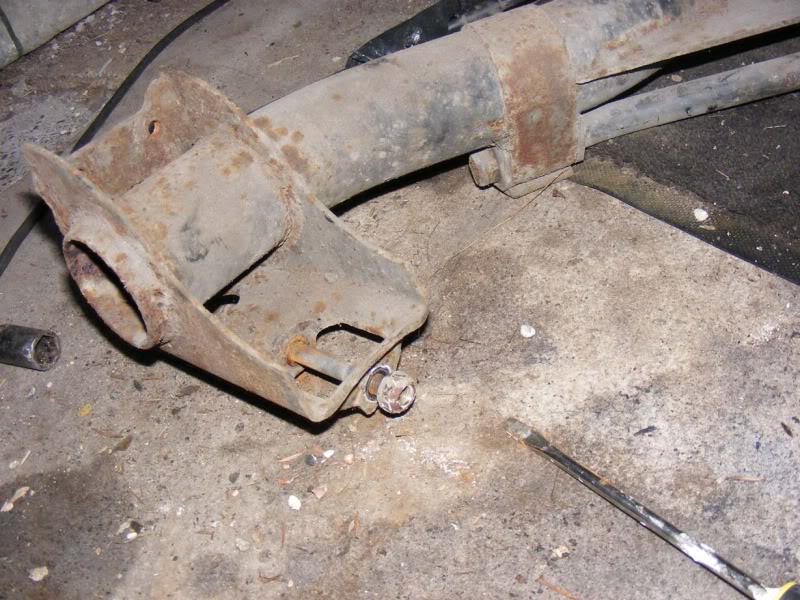
Step 68 - Now you should have a bare subframe. The only things attached are the bushes holding it on (we'll come to those) and the anti-roll bar. If your anti roll bar bushes are worn then simply remove the bar and slide new bushes on (see the front end rebuild guide for details on replacing roll bar bushes)
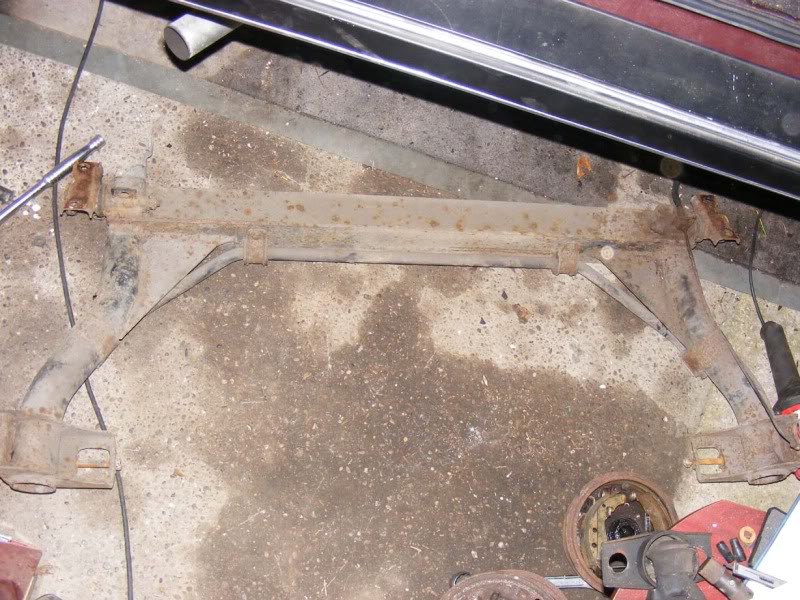
Step 69 - Use a wire brush to remove surface rust and dirt from the subframe (second and third pictures show a before and after of the hole subframe)
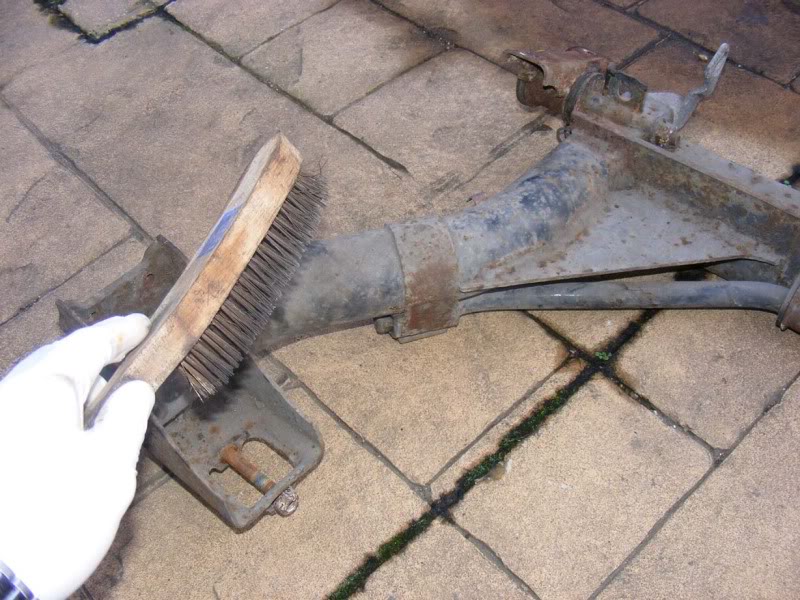
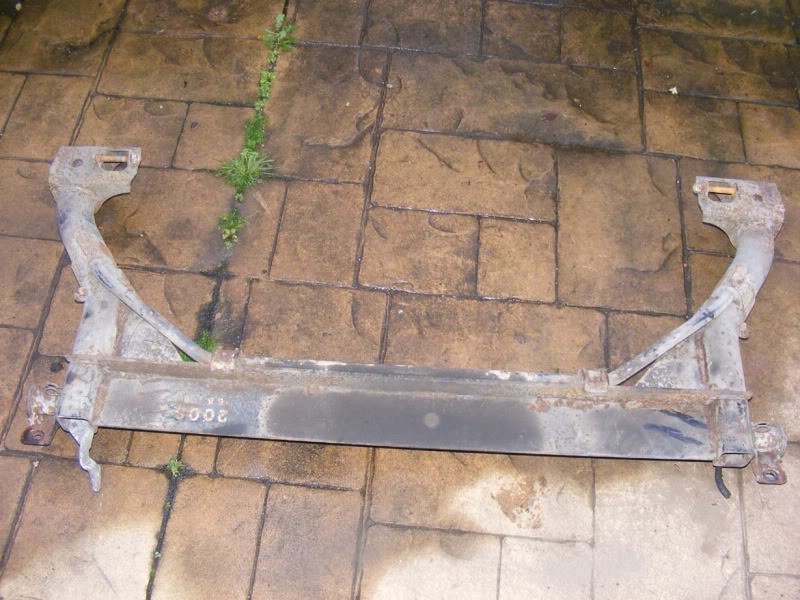
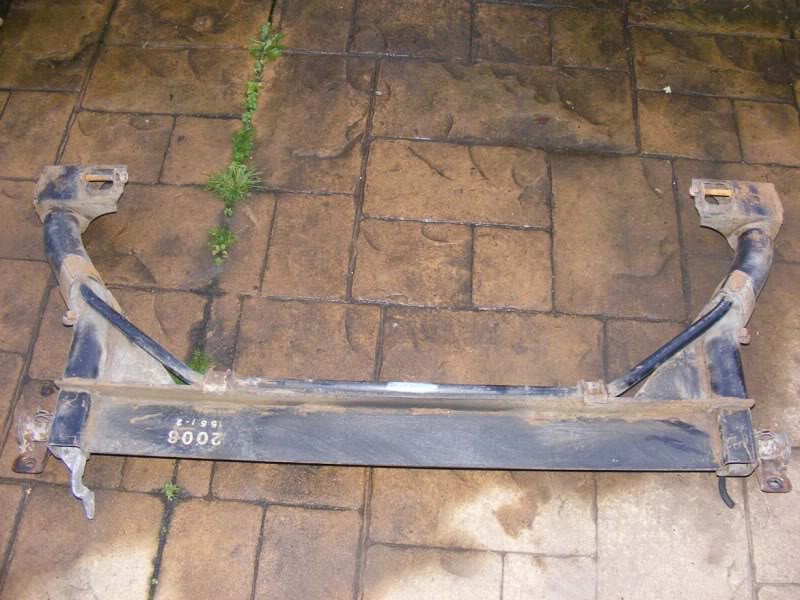
Posted
Settled In

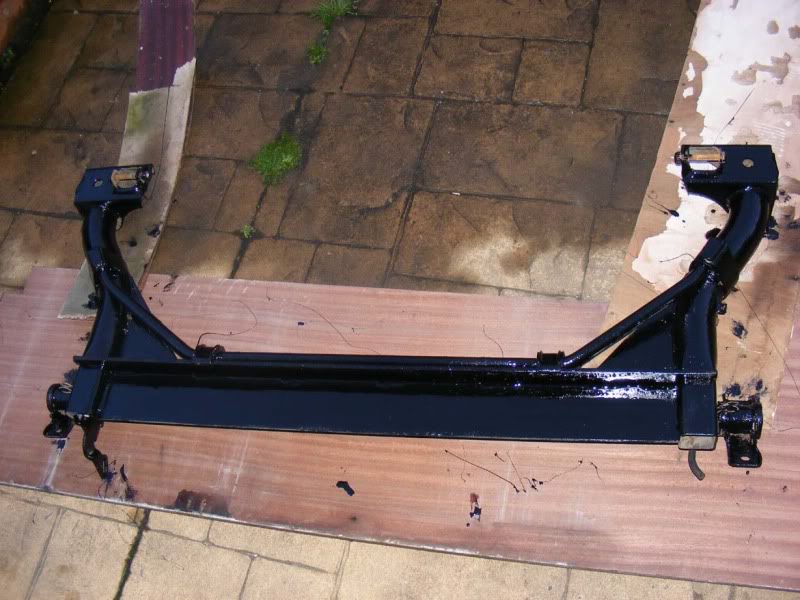
Step 71 - Time to rebuild the shocks and springs now, use a spring compressor (shown is a hydraulic one which will cost you about £70 and is WELL worth it, even if you only do one spring job a year it'll pay for itself quickly - failing that use TWO sets of ordinary clamps). Relieve the tension in the spring
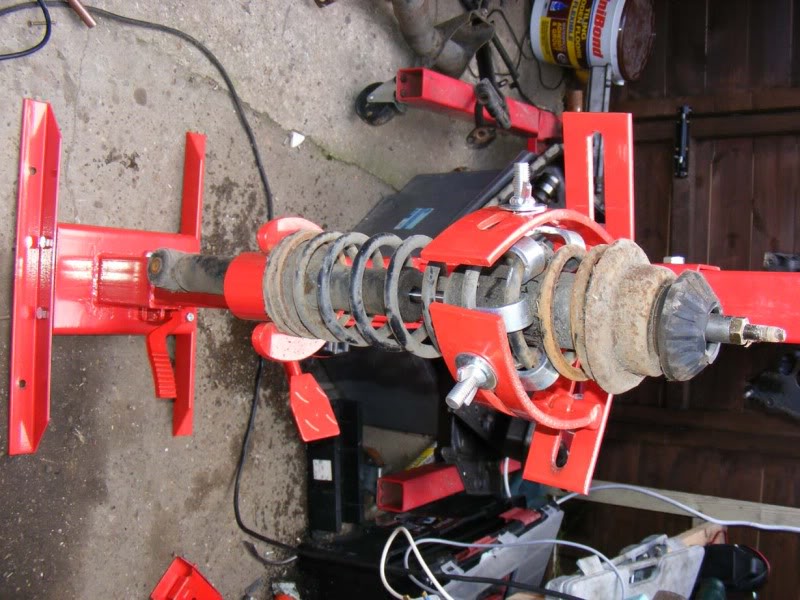
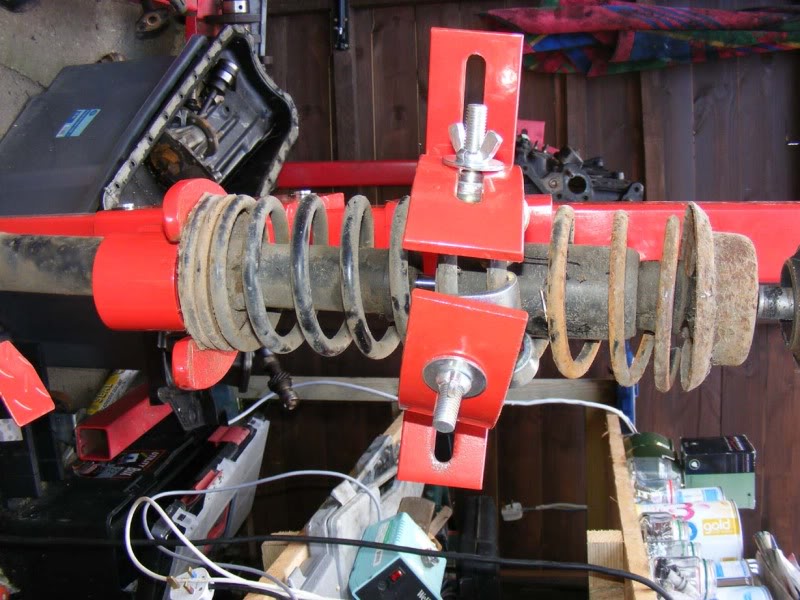
Step 72 - You will be able to pull (and twist) the top mount off
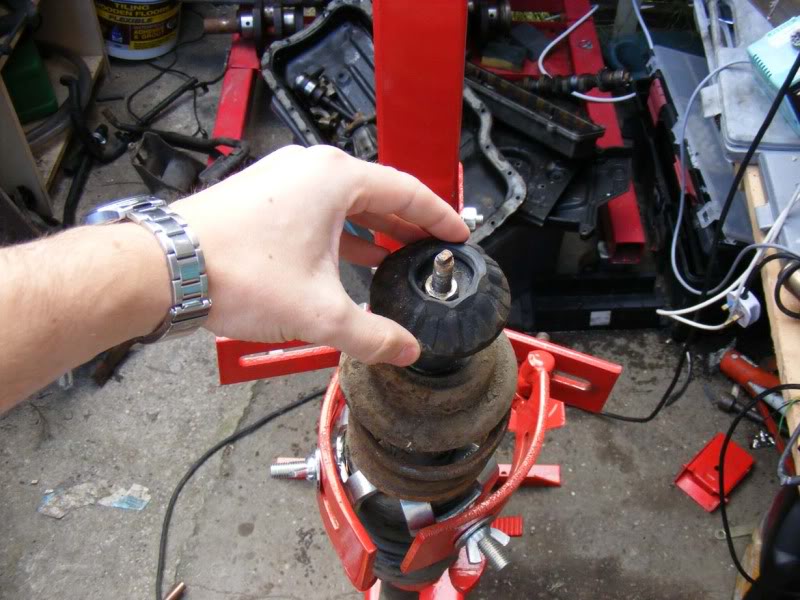
Posted
Settled In

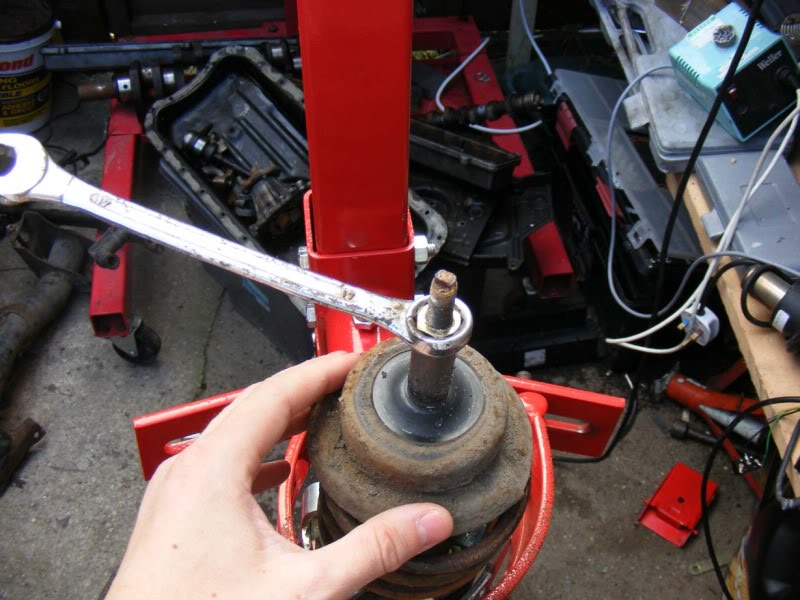
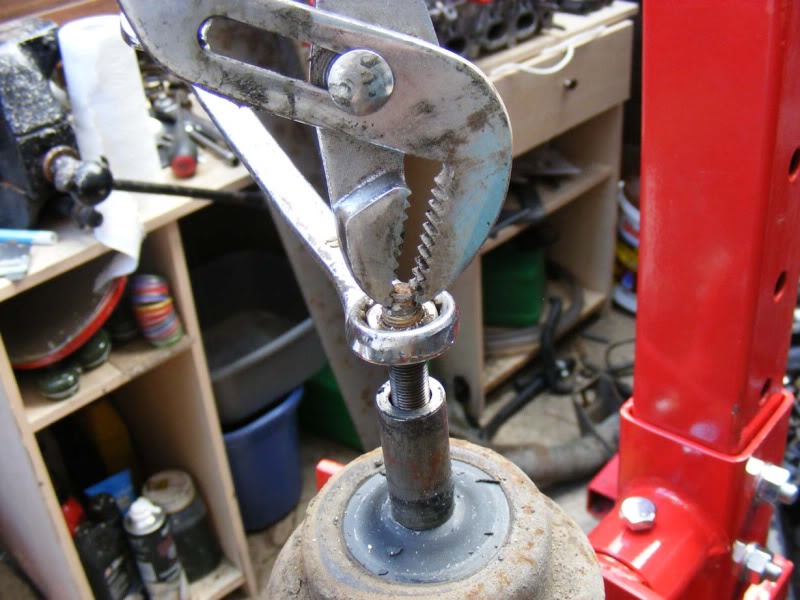
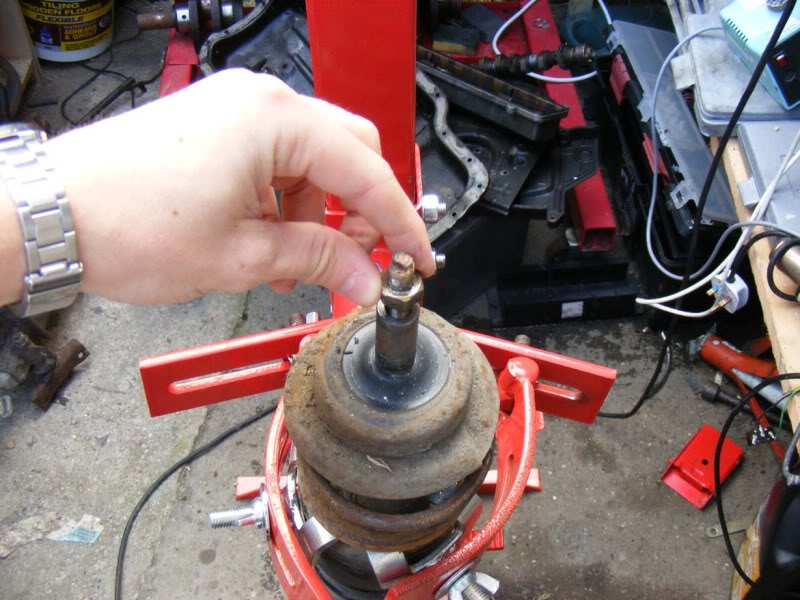
Step 74 - If you find the nut gets stuck at the top where the flats are, hold the spacer directly with mole grips as shown. Be absolutely certain that there is no tension on the spring when you remove the top nut!
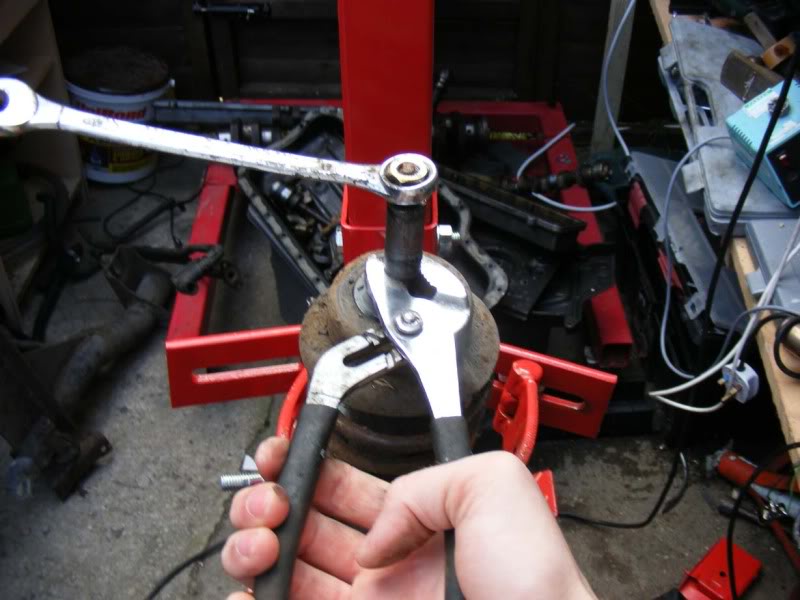
Step 75 - Remove the top nut and spacer
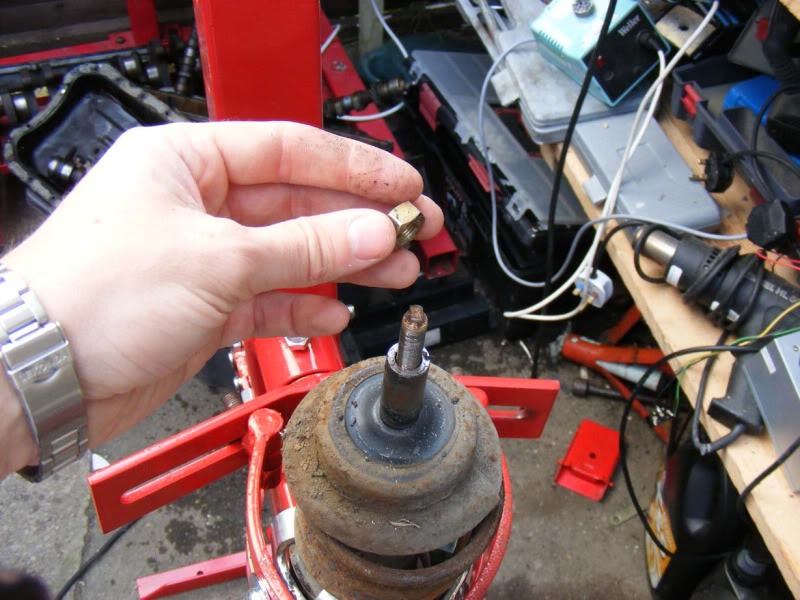
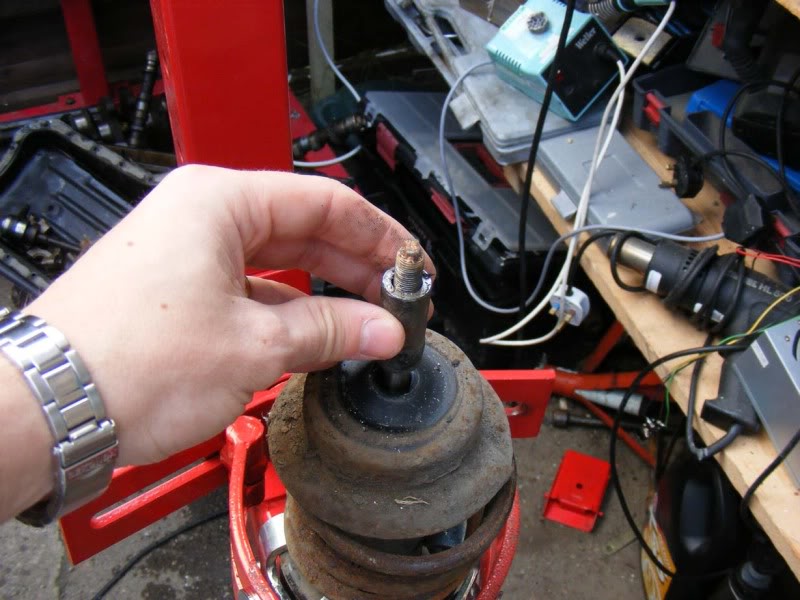
Posted
Settled In

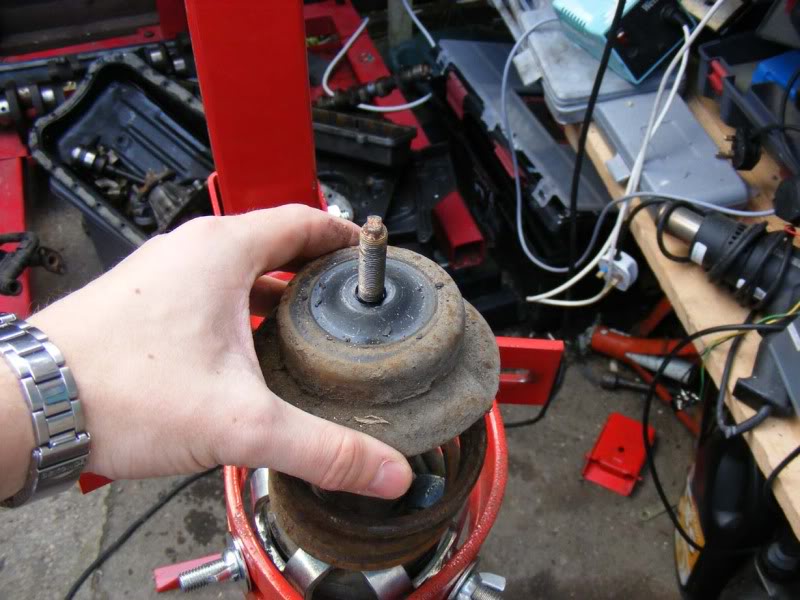
Step 77 - At this point you can relieve the spring tension slowly, very safe and easy with the hydraulic compressors
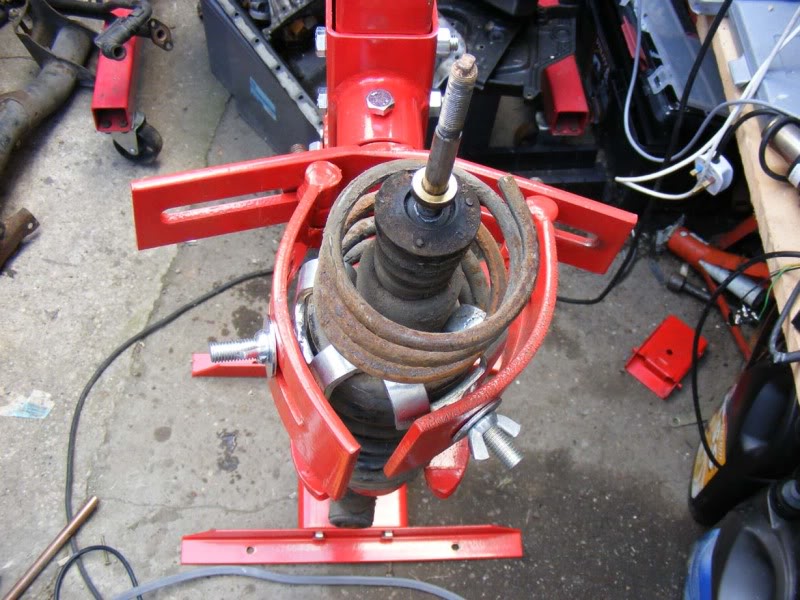
Step 78 - Once the spring tension is released, remove and discard the old spring
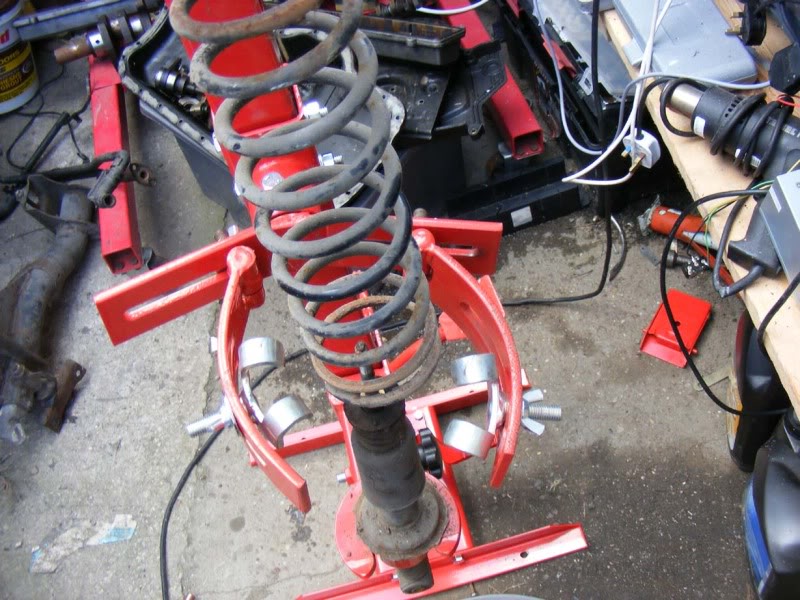
Posted
Settled In

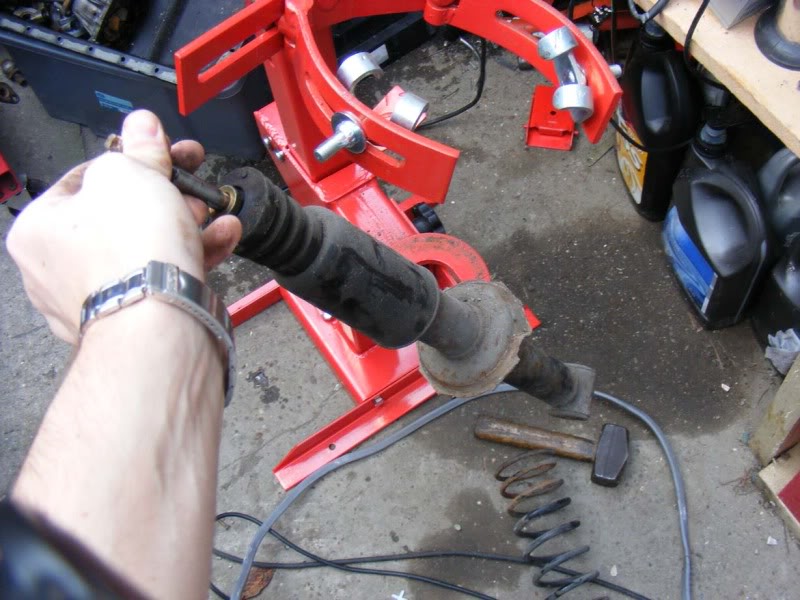
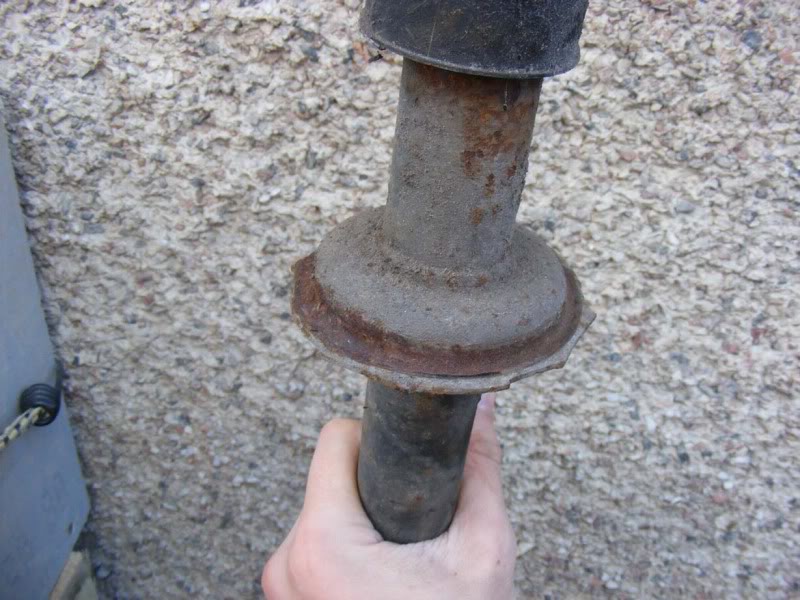
Step 80 - As always, keep everything in a neat order so you know what goes where when it comes to reassembly
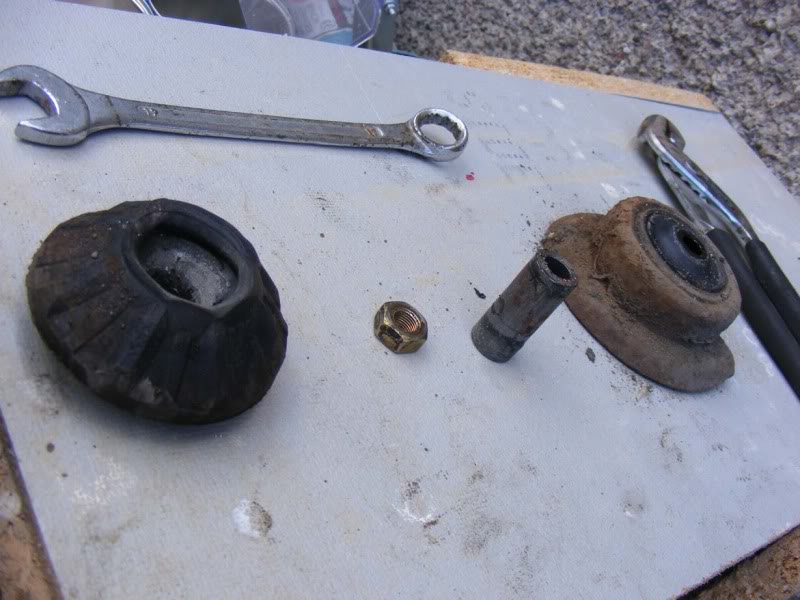
Step 81 - Grab yourself a shiny new shock and prepare to reassemble
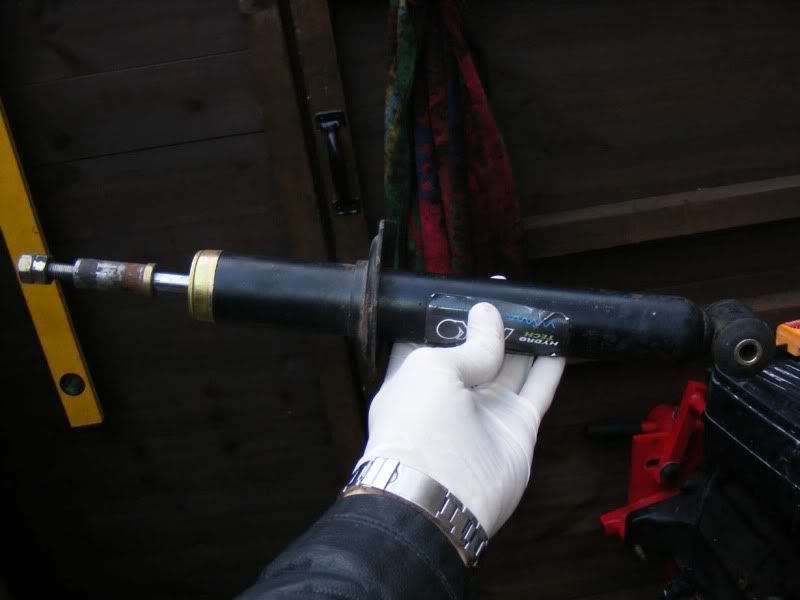
Posted
Settled In

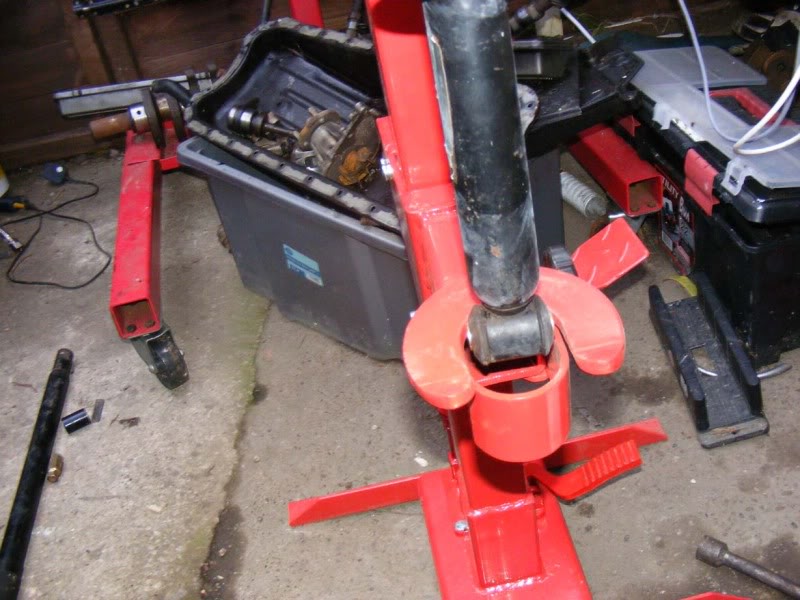
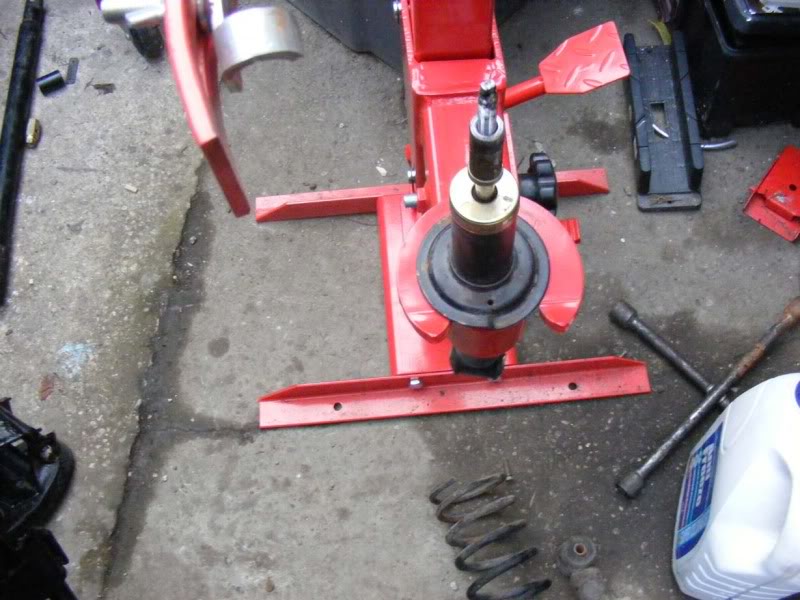
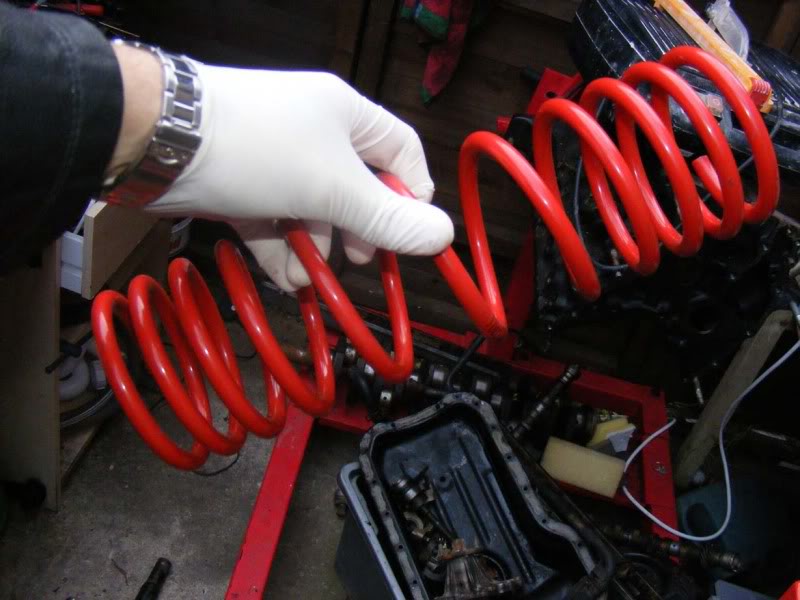
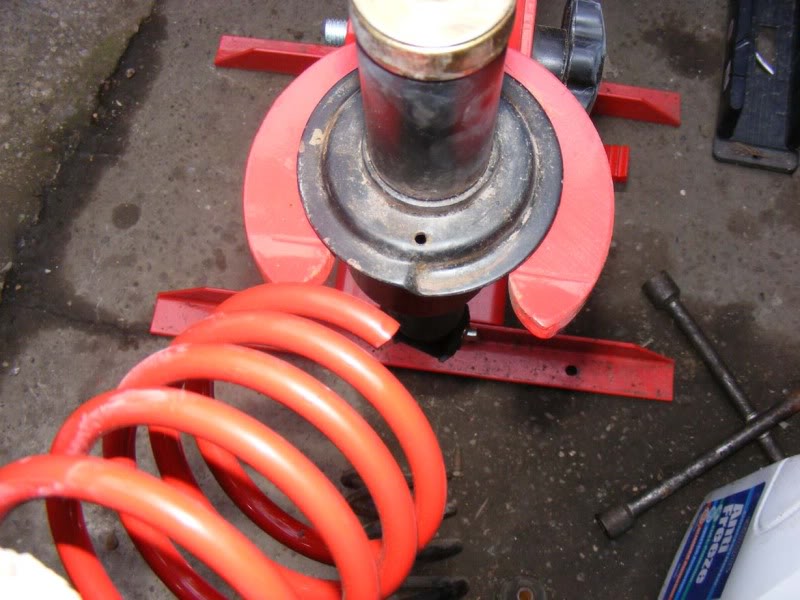
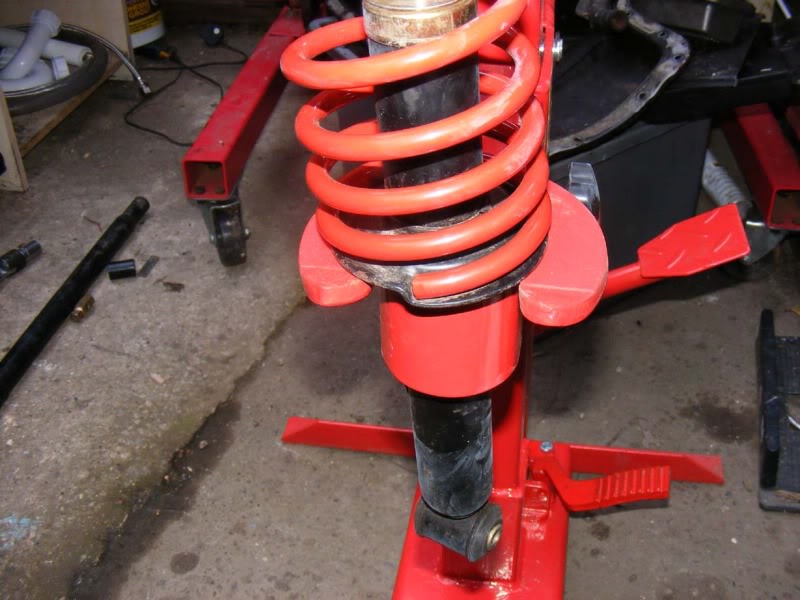
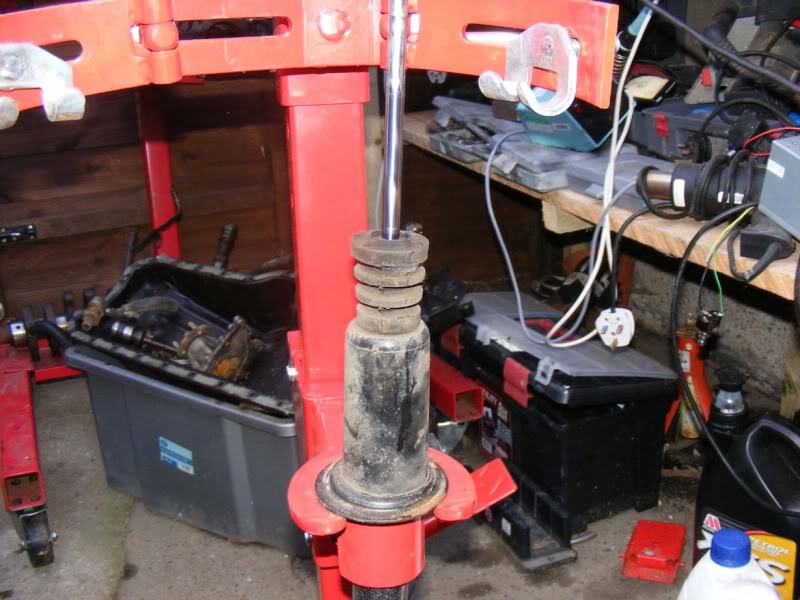
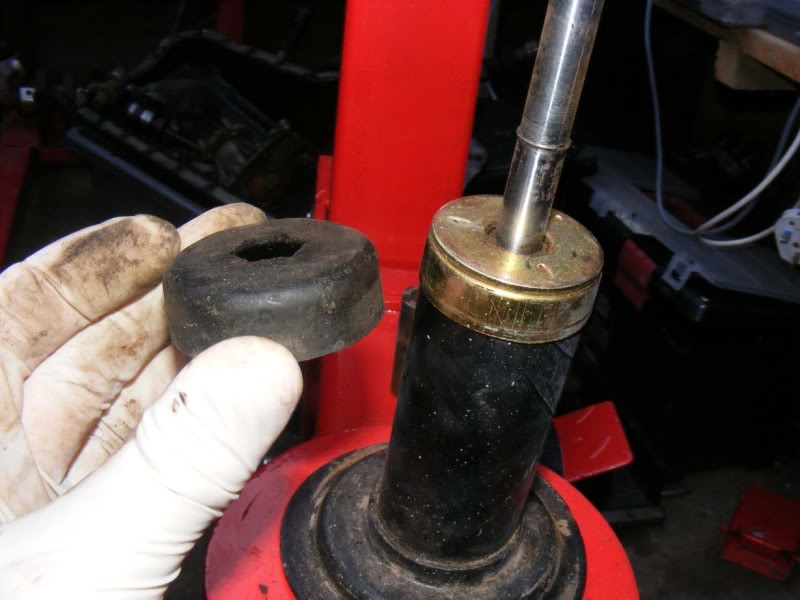
Posted
Settled In

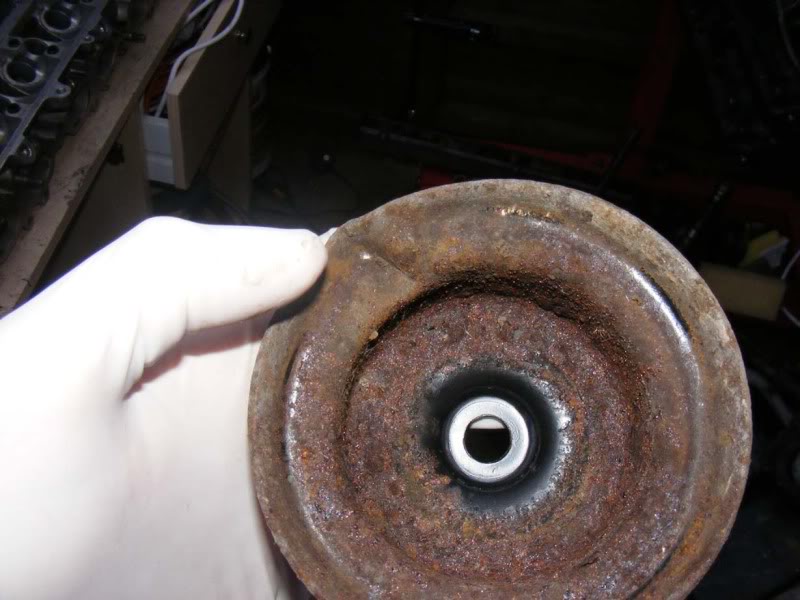
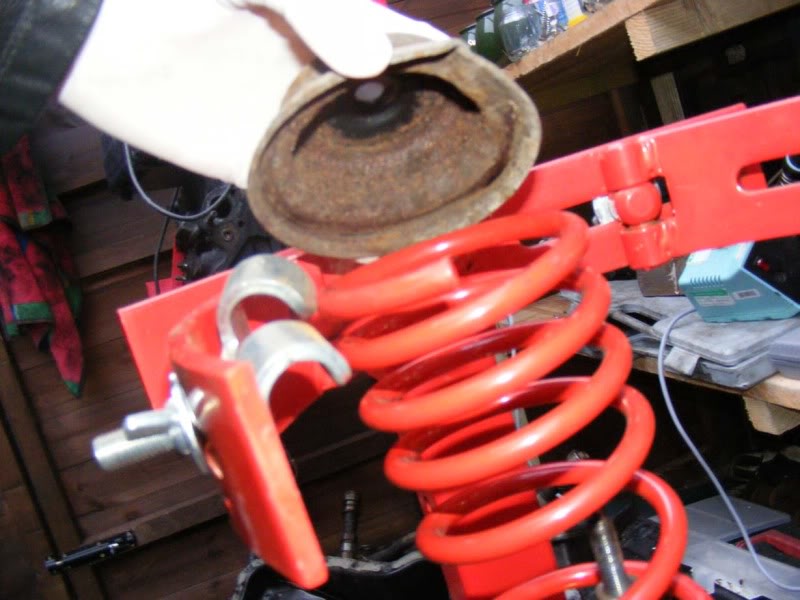
Step 84 - Hook the metal clamps over the spring near the top
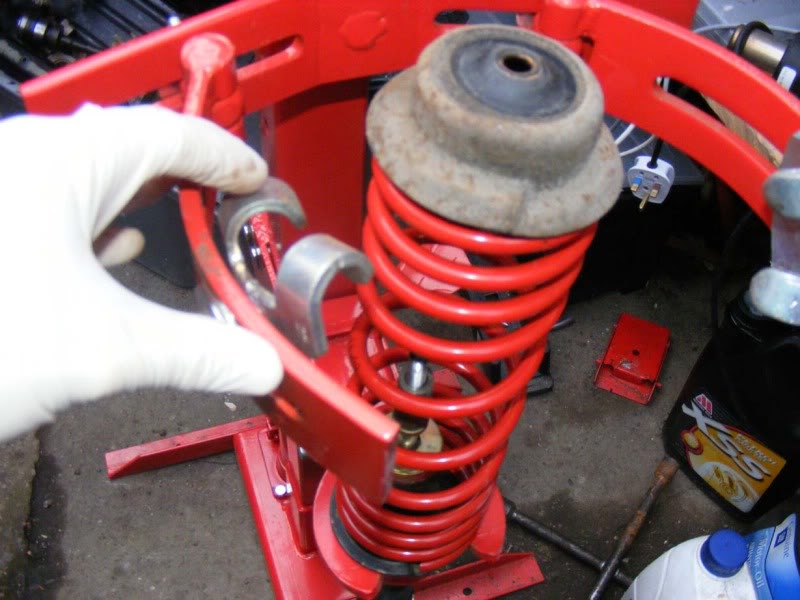
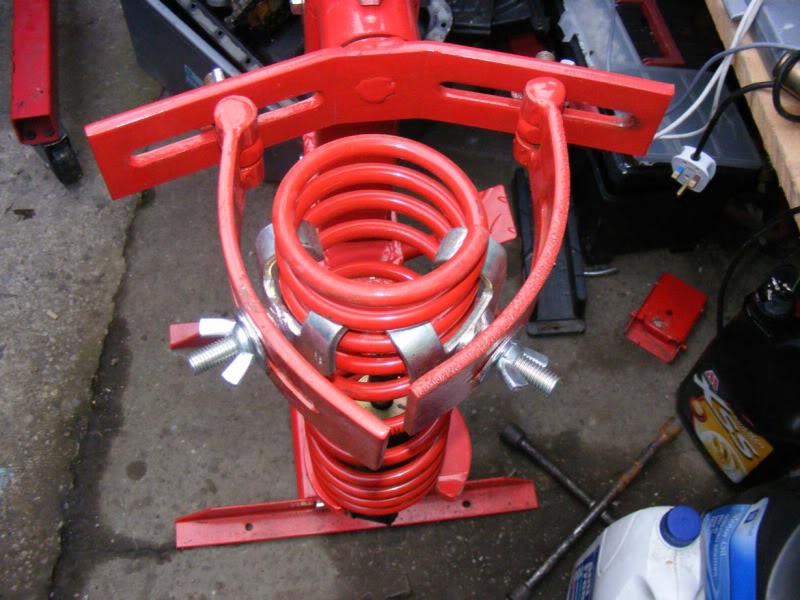
Posted
Settled In

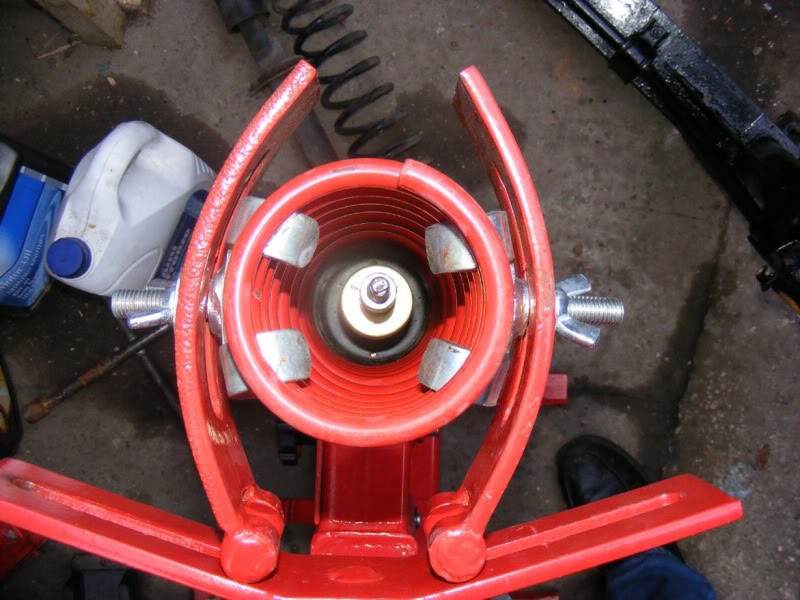
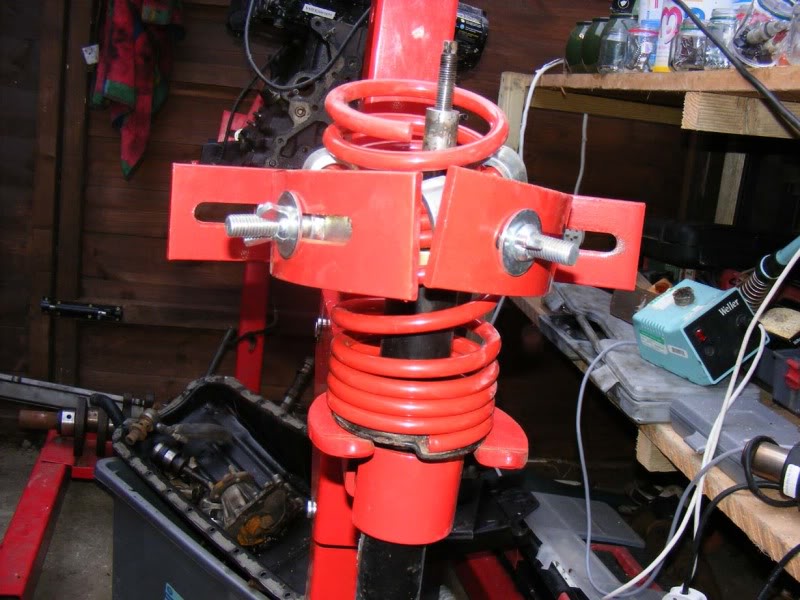
Step 86 - Fit the washer, spacer and top nut. You will need to hold the flats again when it comes to tightening the top nut
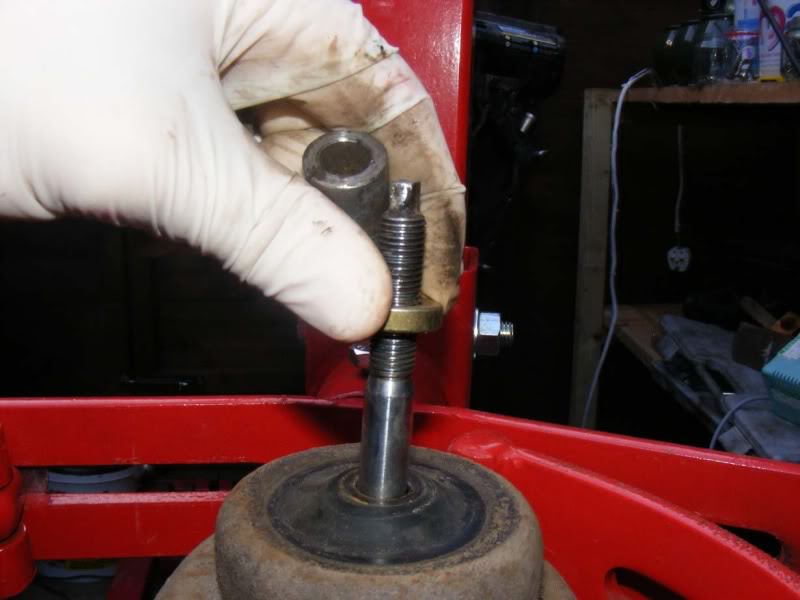
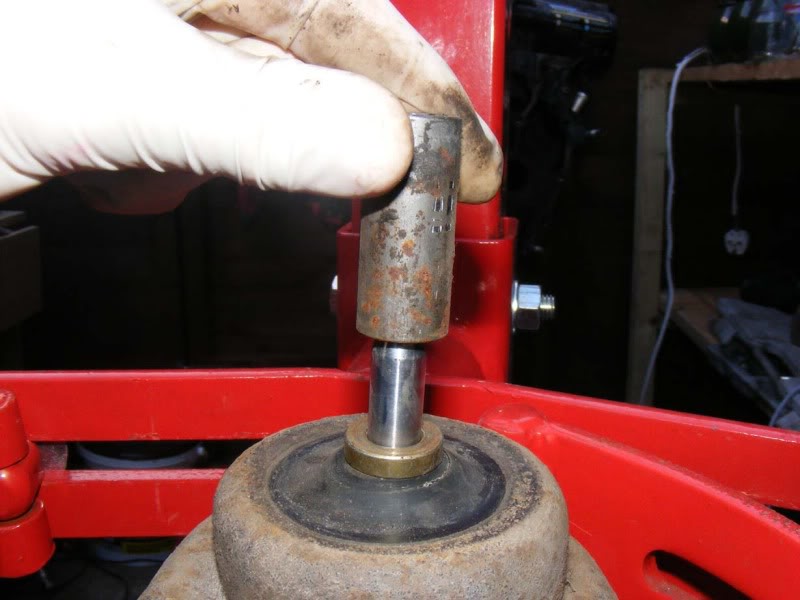
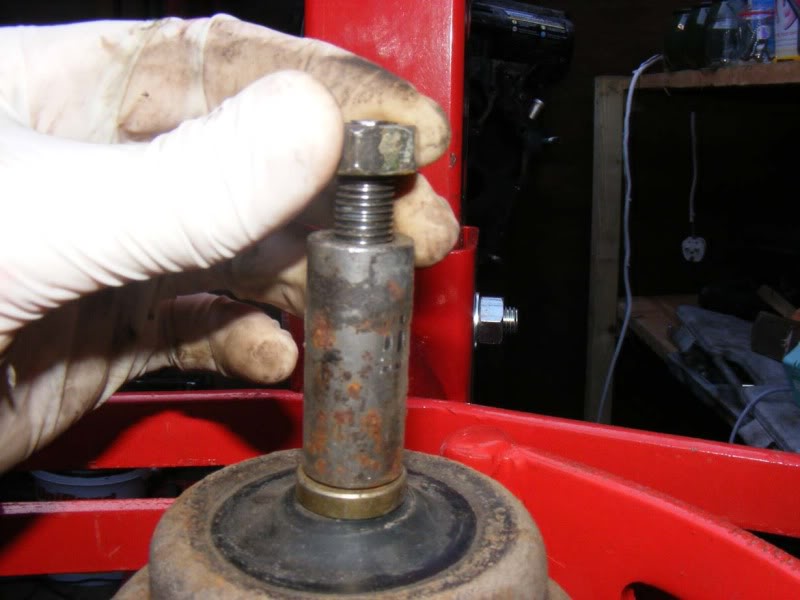
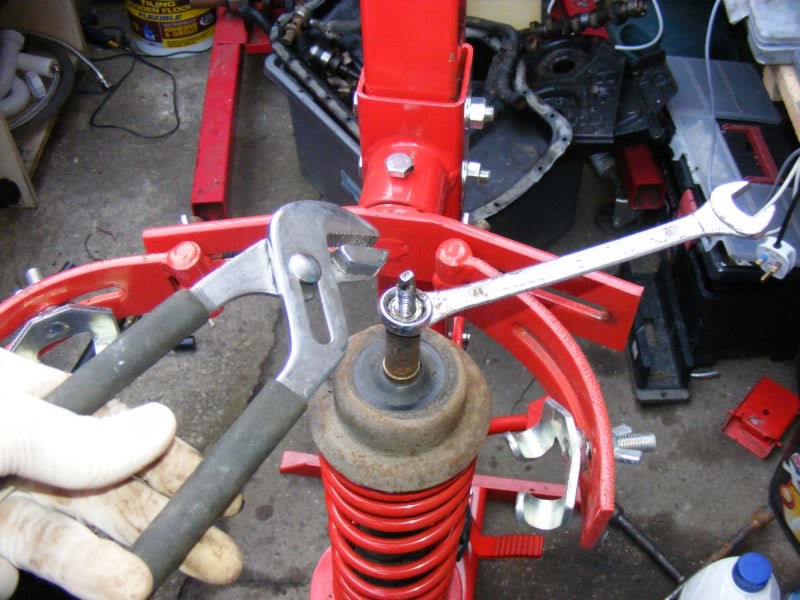
Posted
Settled In

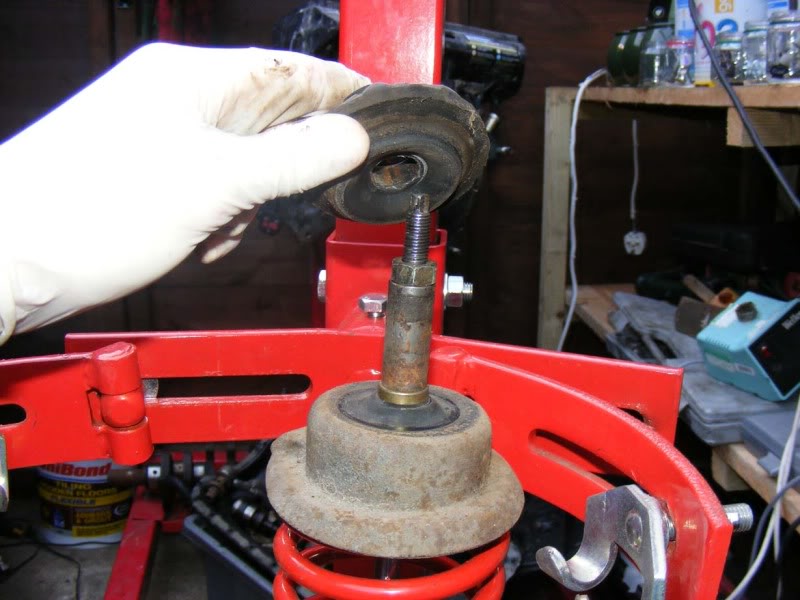
Step 88 - Relieve the spring tension and remove shock/spring assembly
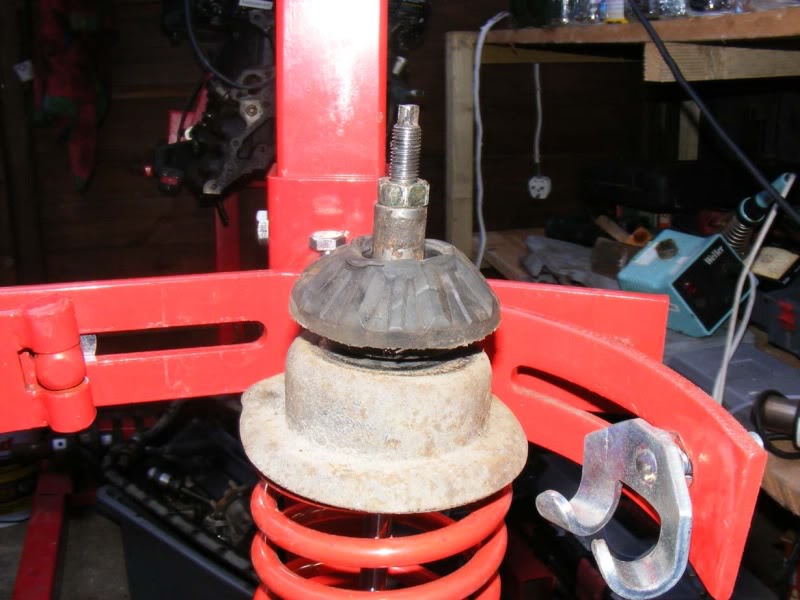
Step 89 - Repeat for the other side!
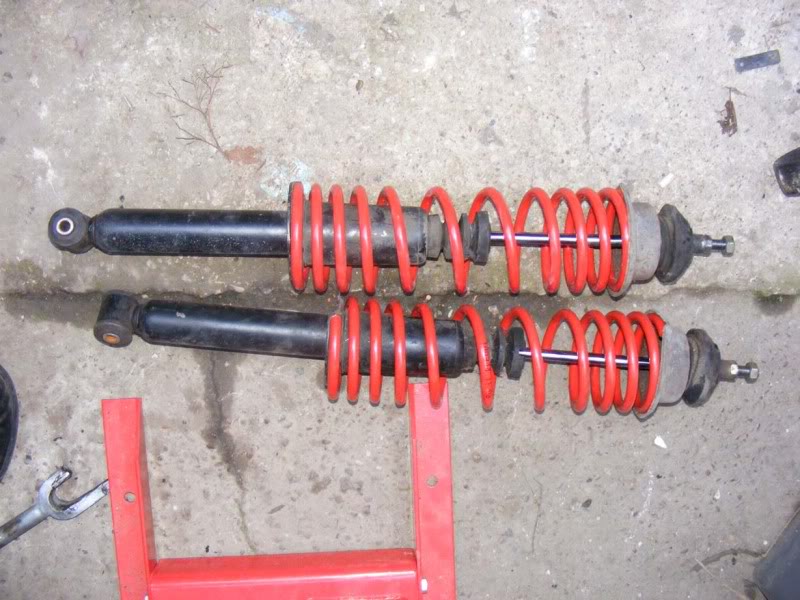
Posted
Settled In

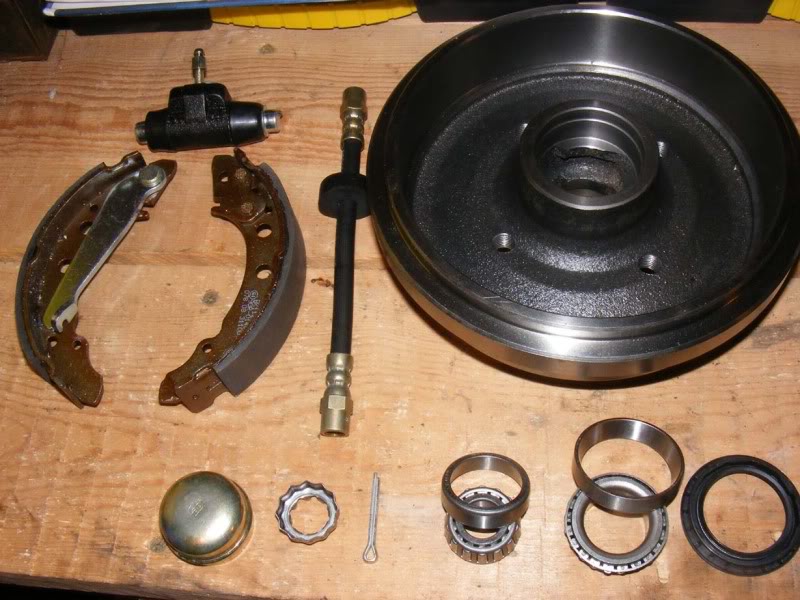
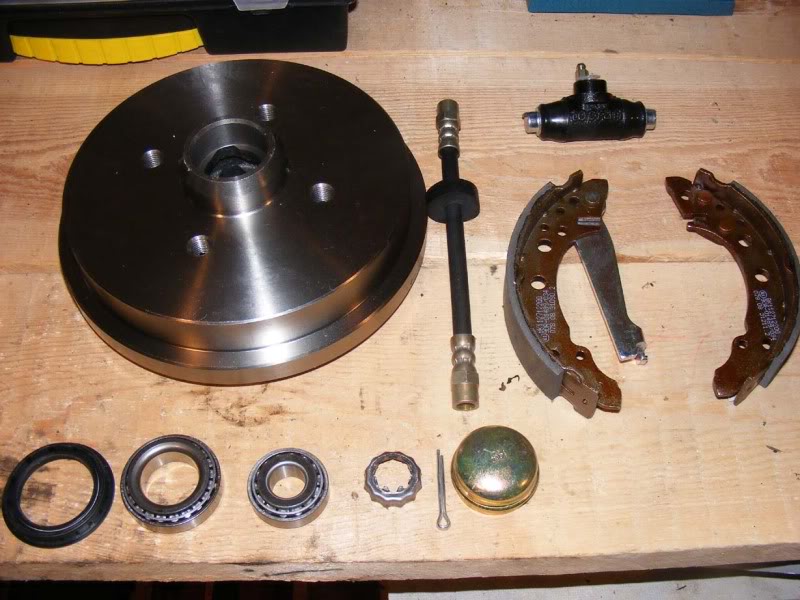
Step 91 - We already stripped the backplate earlier so we will now freshen it up a bit (you can replace but usually not required). Clean off any grease from the threads and shaft
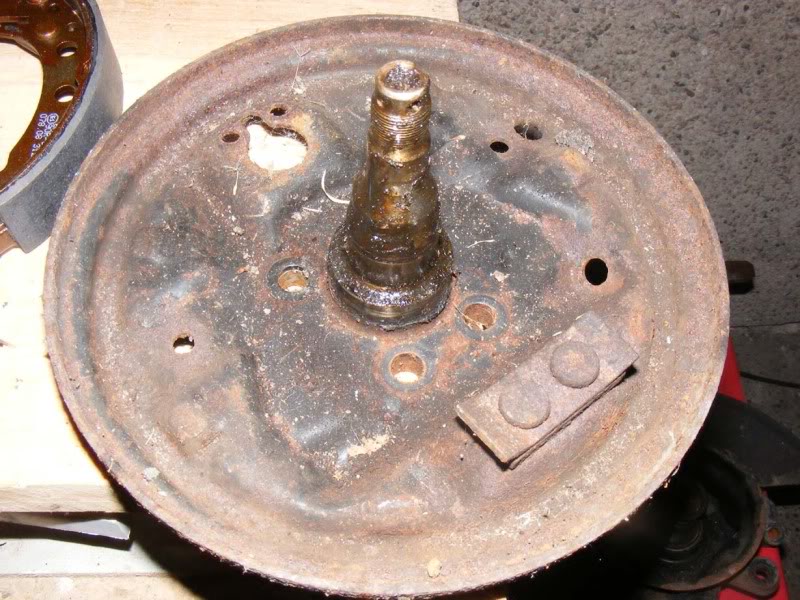
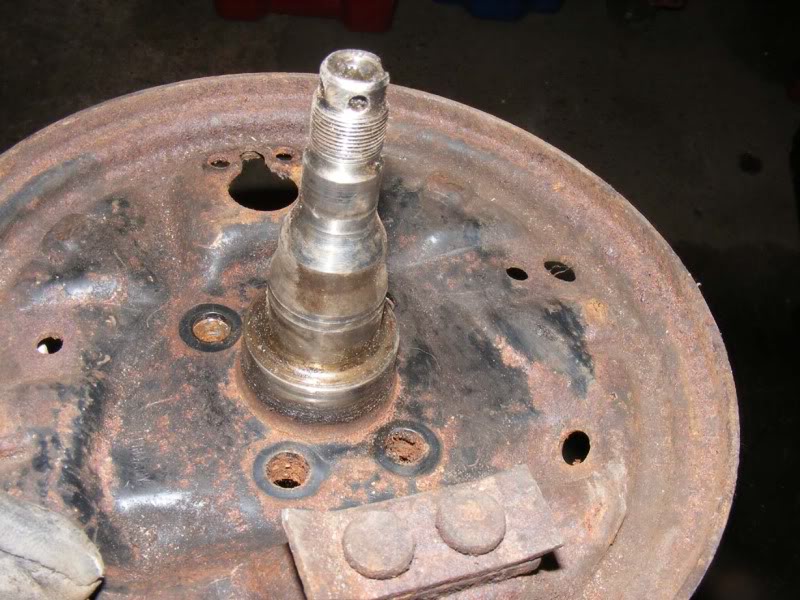
Posted
Settled In

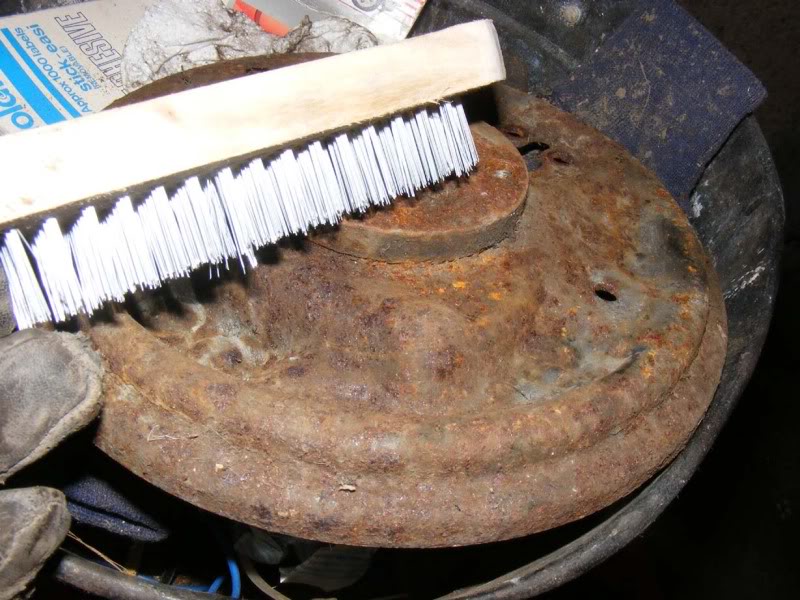
Step 93 - When you have finished you will probably have something quite orange like this
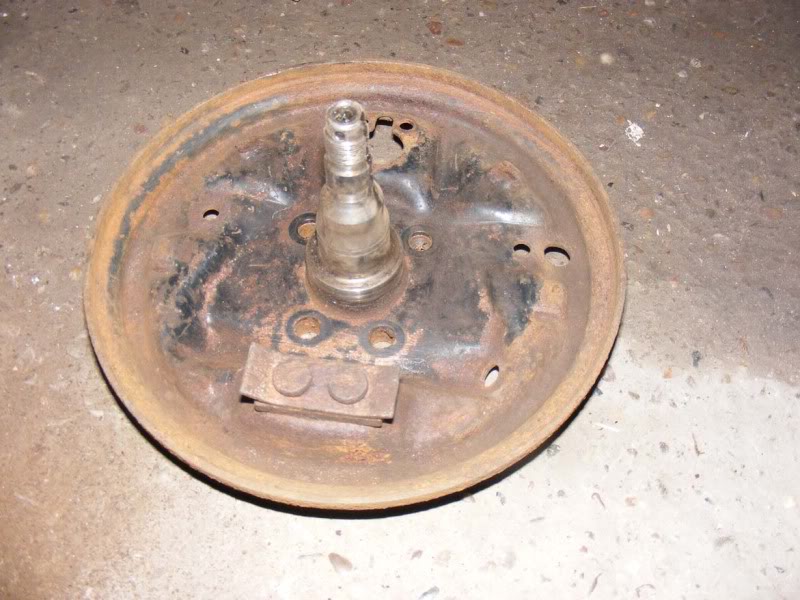
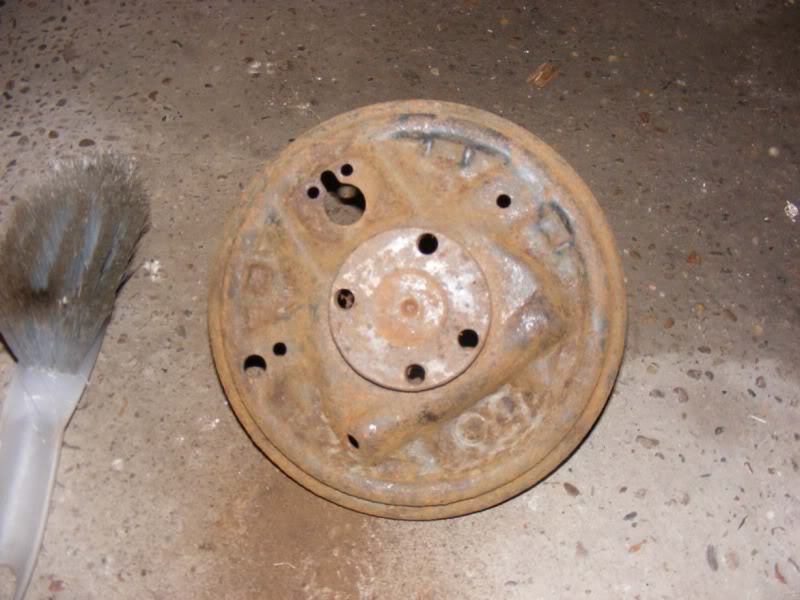
Step 94 - Time for some more Hammerite to bring it back to black and protect the backplate from the elements
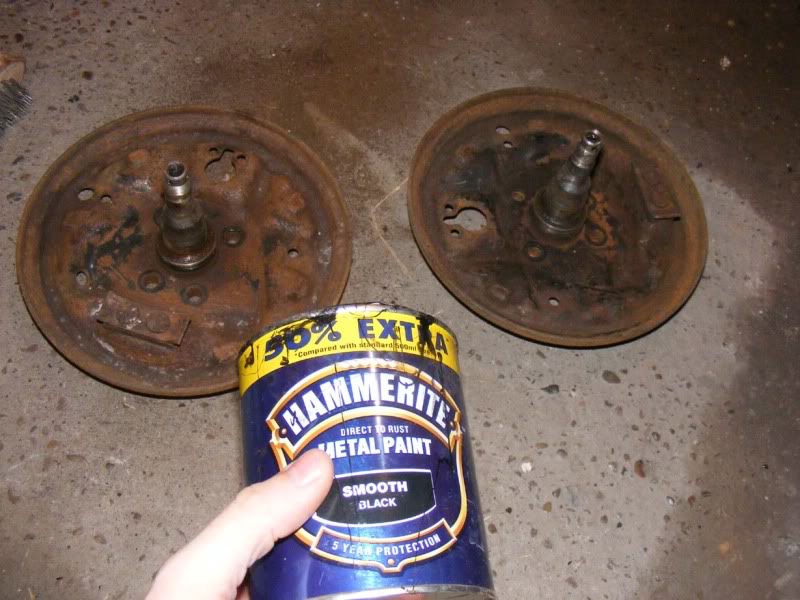
Posted
Settled In

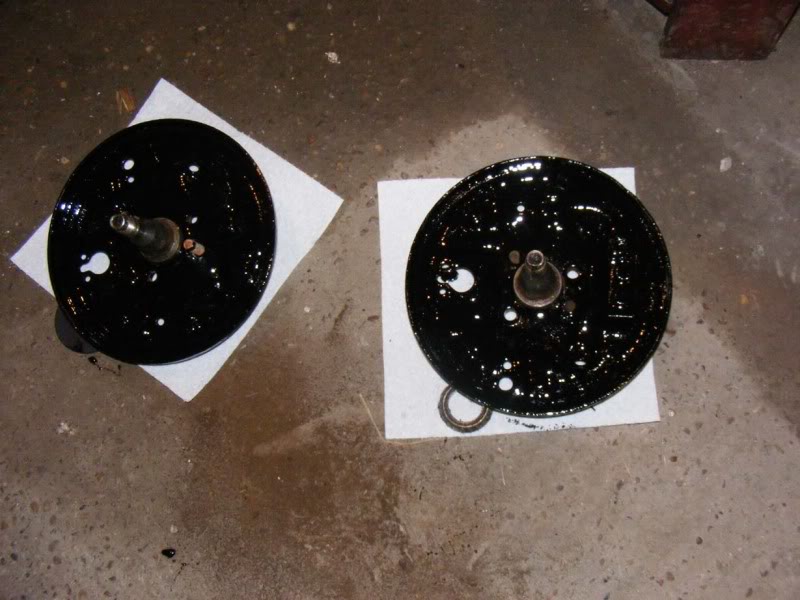
Step 96 - Now the bearings, these consist of two parts, the tapered piece with all the little roller bearings in it and the 'race' that it sits in and spins. The hard bit is making the race go in the hub because it is a very tight interference fit so you may want to pass it to a garage for these to be pressed in (don't pay more than £10-£15 though)
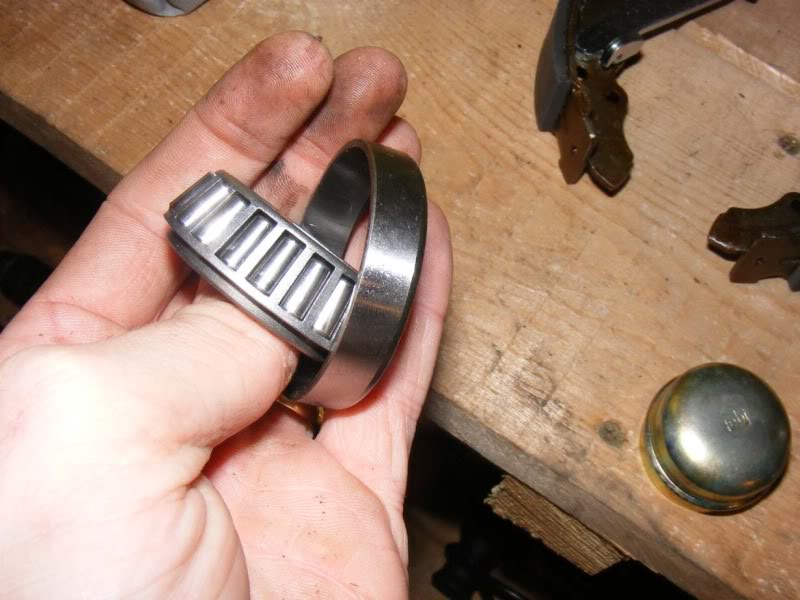
Step 97 - If you're a die hard like me then you can do it yourself with a little brain and a little brawn! The race needs to sit in the hub as shown (picture 1 shows inner and picture 2 outer)
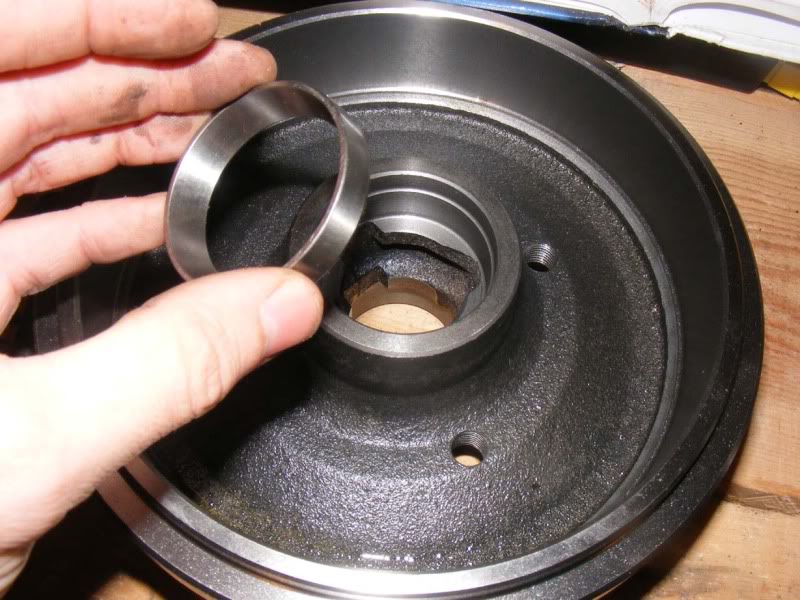
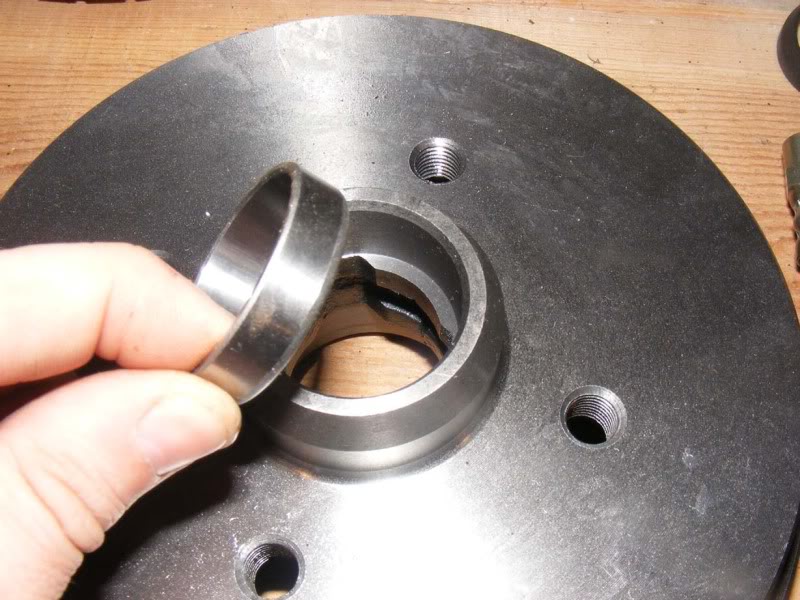
Posted
Settled In

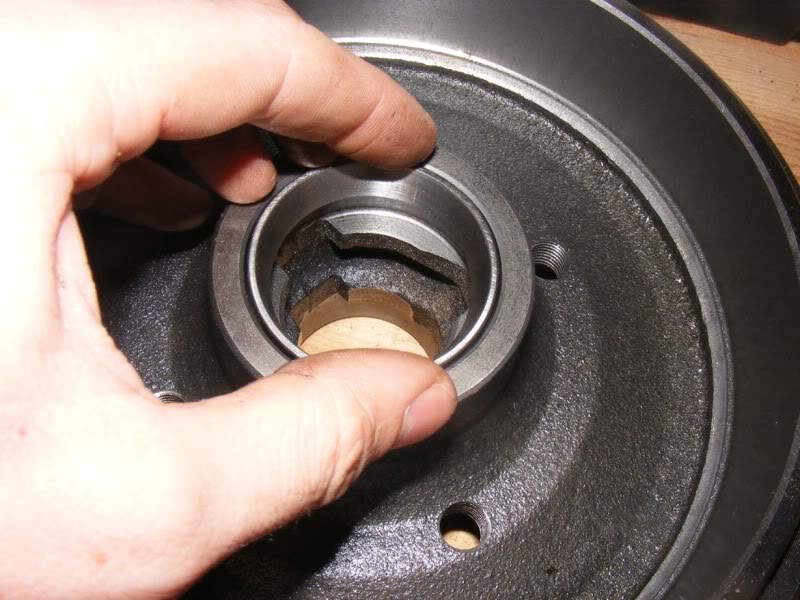
Step 99 - Clean up an old inner and outer bearing that you removed earlier
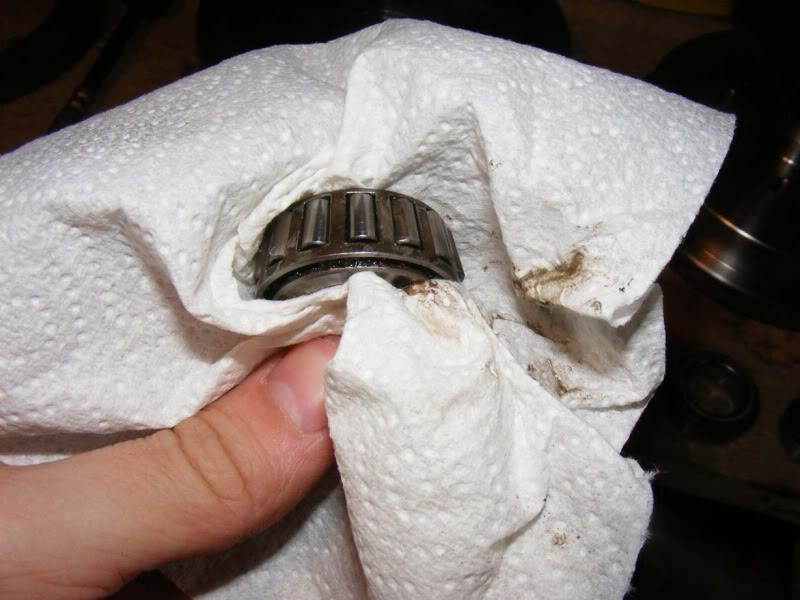
Step 100 - Pop the old bearing into the race (which is just placed over where it will sit in the picture)
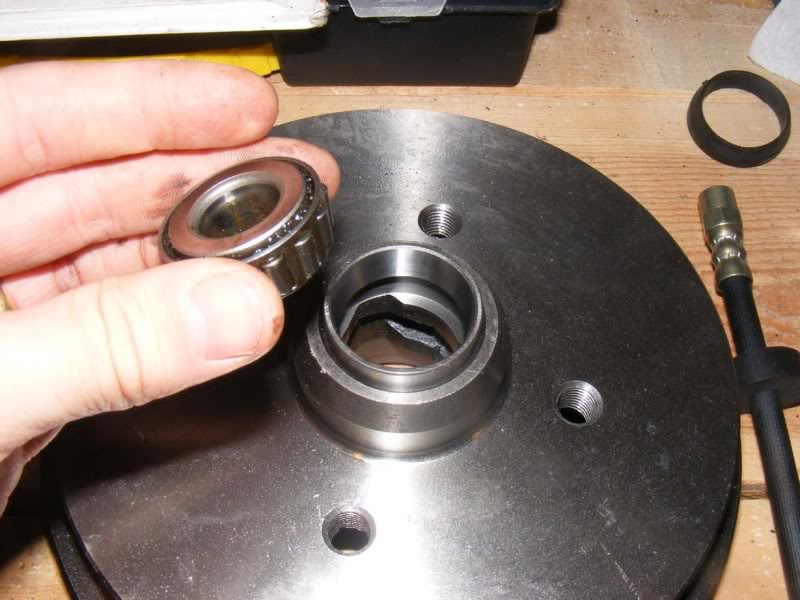
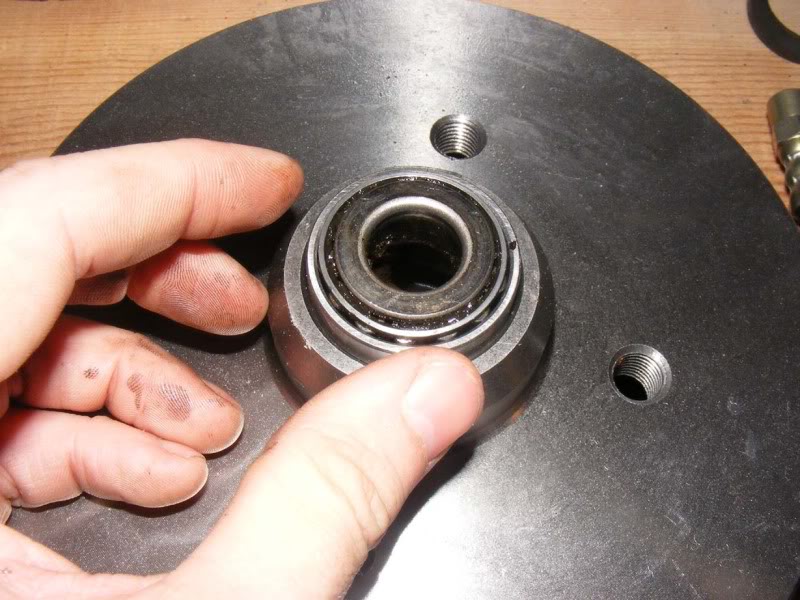
Posted
Settled In

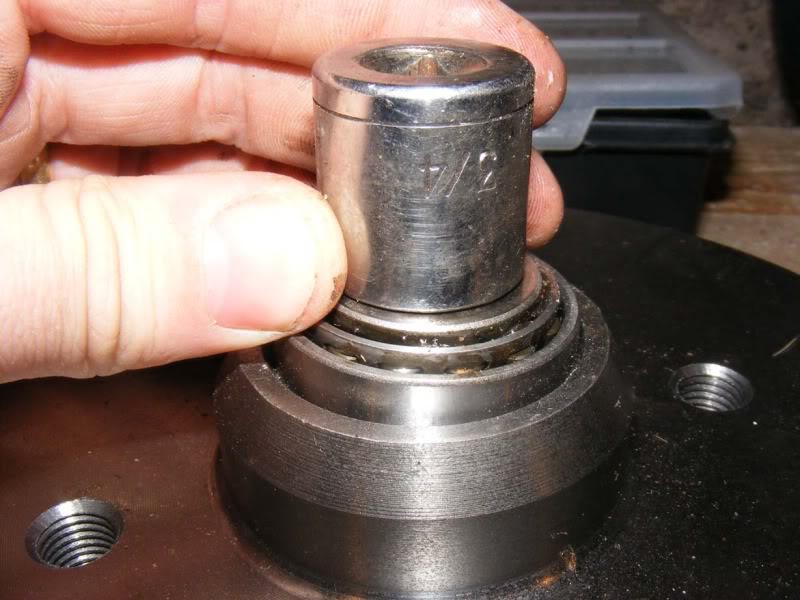
Step 102 - Do the same for the inner bearing (the bigger one), a 28mm is what I chose
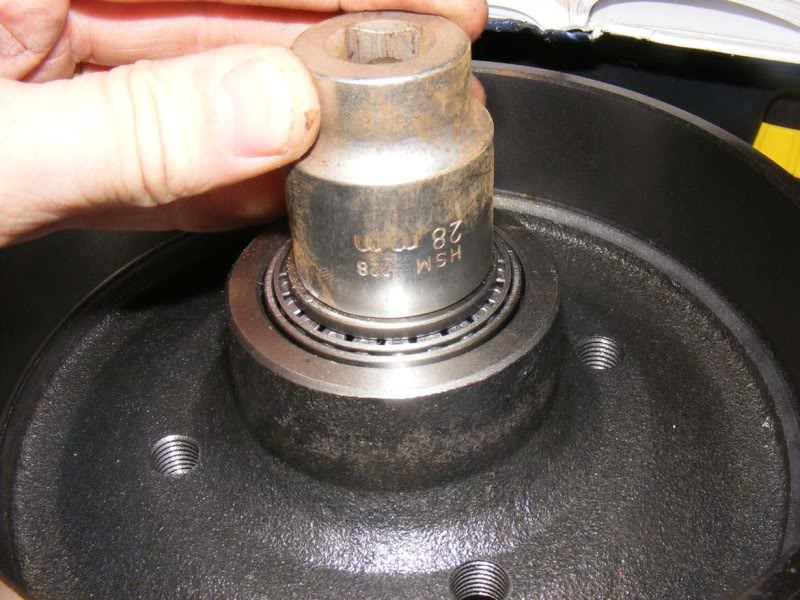
Step 103 - Now where we get a bit clever, cut the bottom of an old plastic bottle
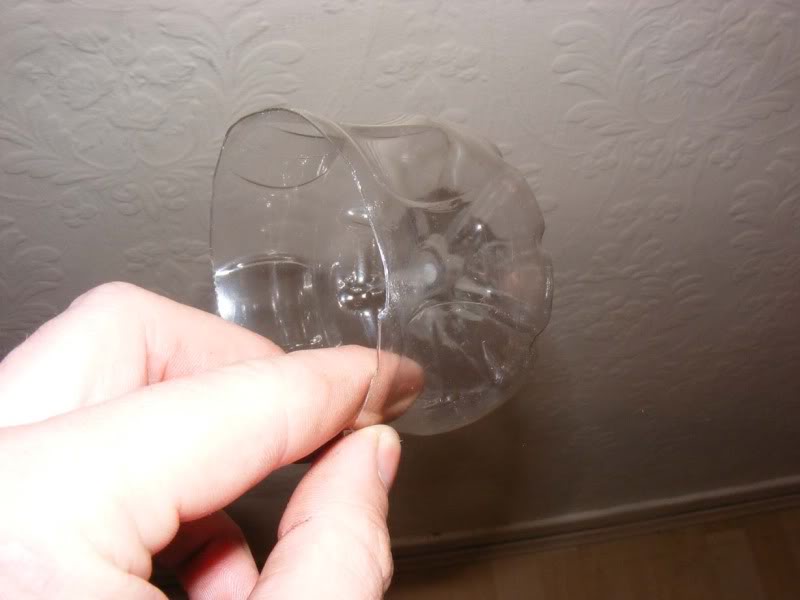
Posted
Settled In

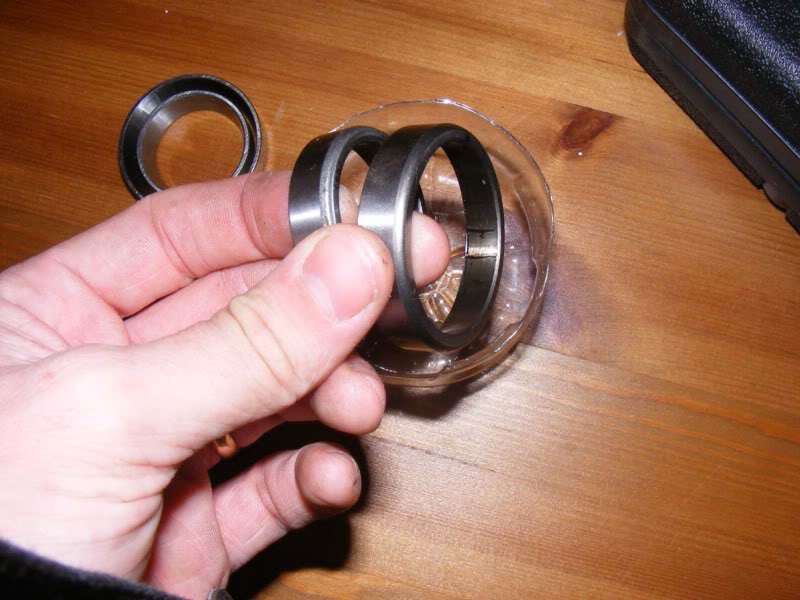
Step 105 - Fill with ordinary motor oil which will later act as a lubricant and stop them from freezing (read on …)
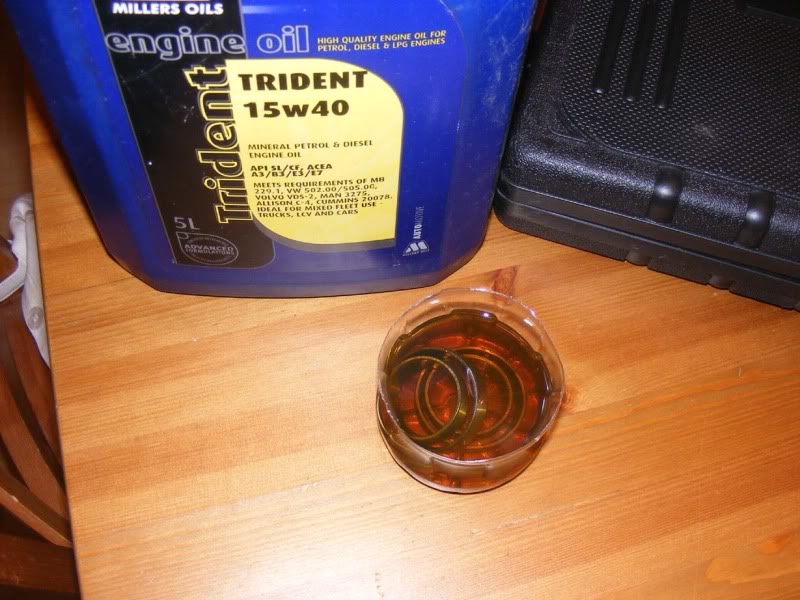
Step 106 - Put the races in your home freezer and leave them for a good few hours or overnight, this will chill them and cause the metal to shrink slightly
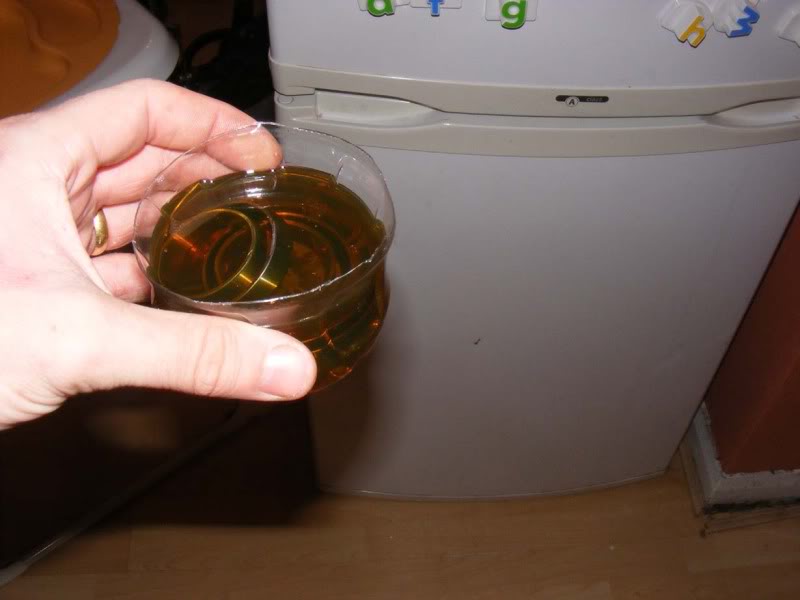
Posted
Settled In

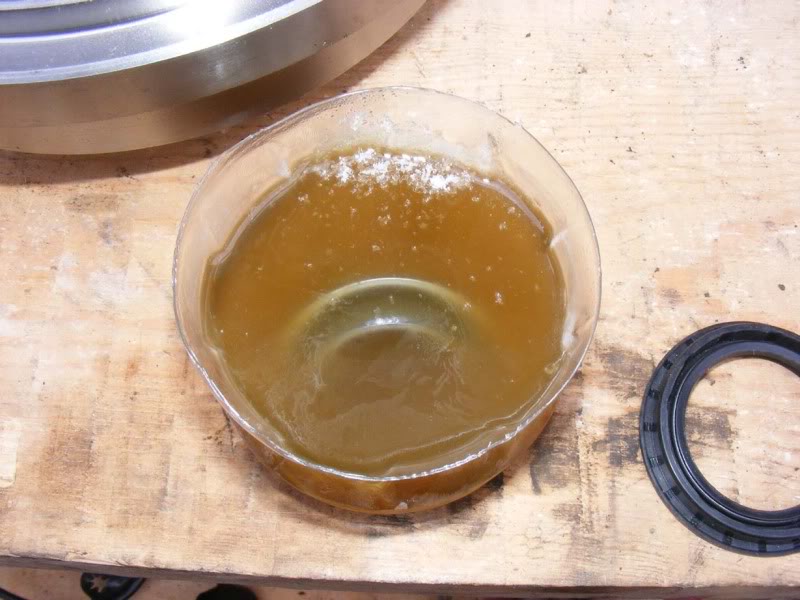
Step 108 - Remove one of the OUTER (smaller) bearing races and place onto the hub
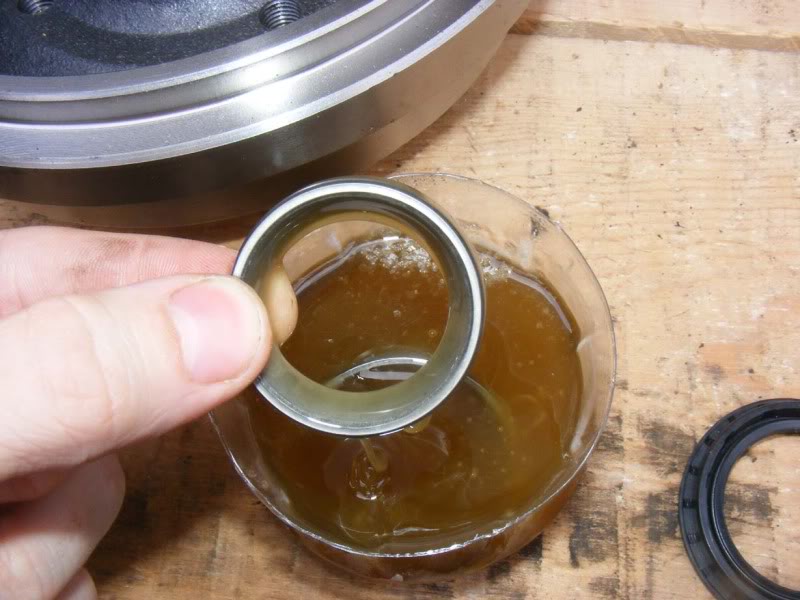
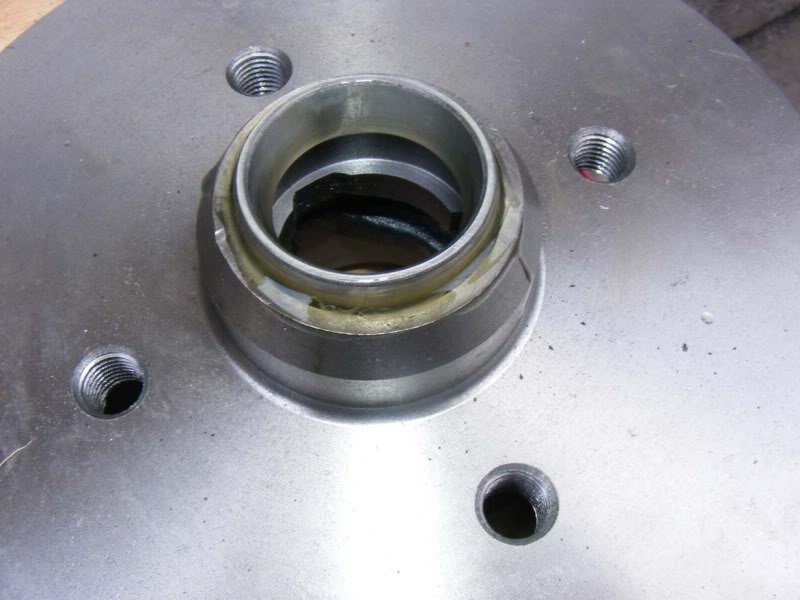
Step 109 - Now put the OLD bearing you cleaned up earlier into the race
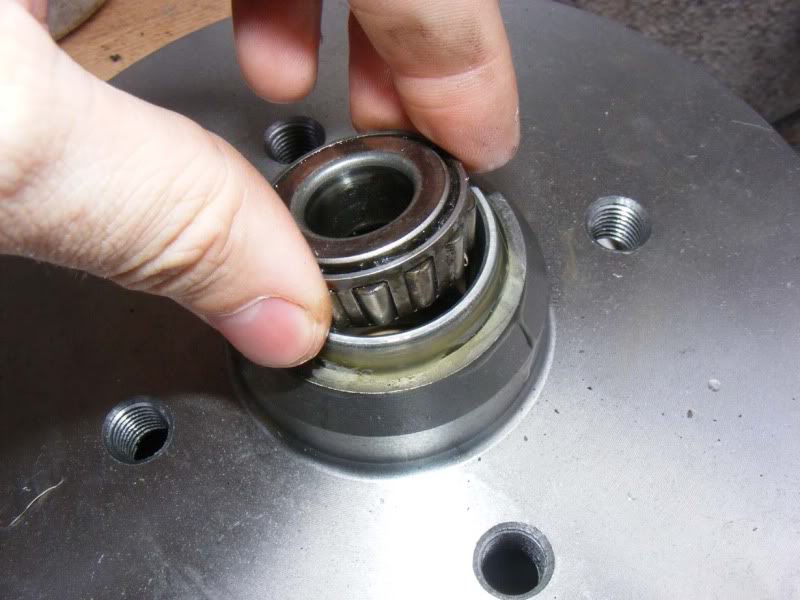
Posted
Settled In

Some tips for you:
1. Don't be shy, smack it hard with a big hammer. Don't let your blow 'bounce' once you hit, ensure you have a solid push after you impact
2. Make sure that the race is square at all times, it is really important
3. Hold the socket you are hitting, you might want gloves on if you aren't a good shot
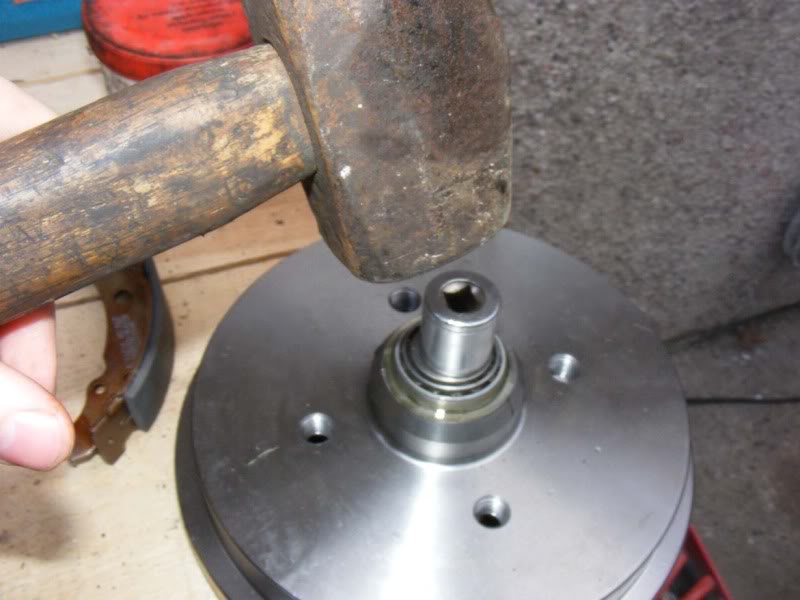
Step 111 - Drive it all the way home until you can remove the bearing and see no gap between the race and the flange in the hub. The third picture shows it fully seated from behind, wipe away excess oil once you have finished
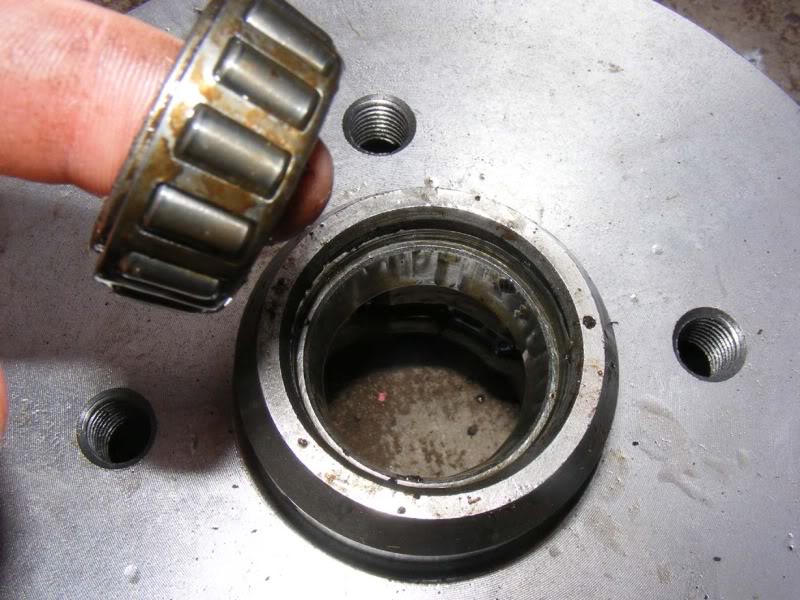
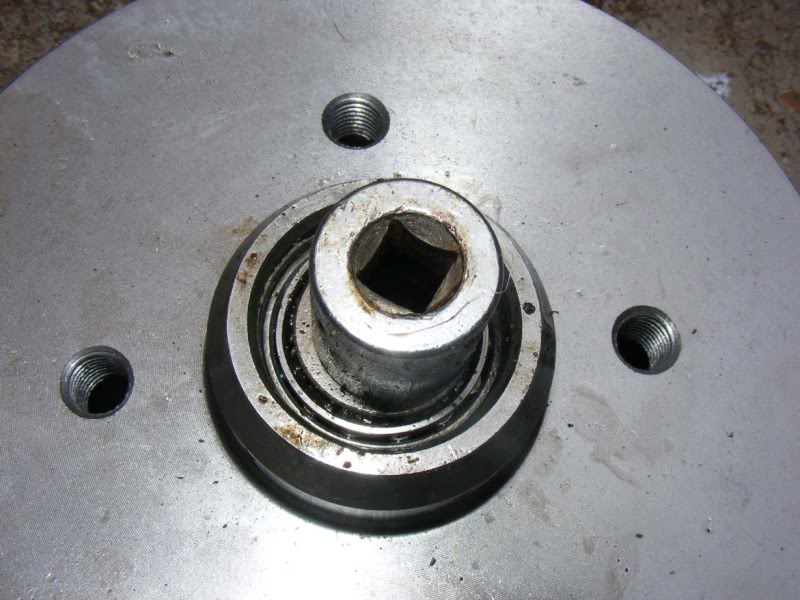
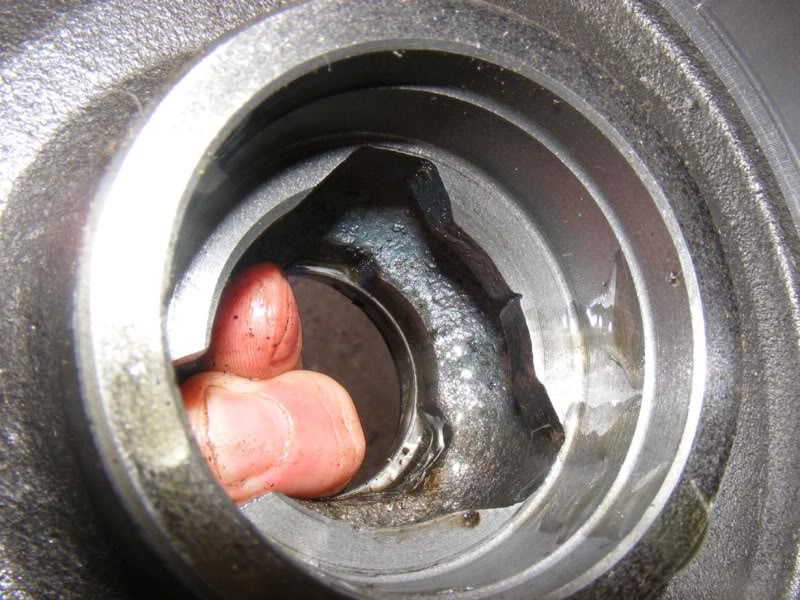
Posted
Settled In

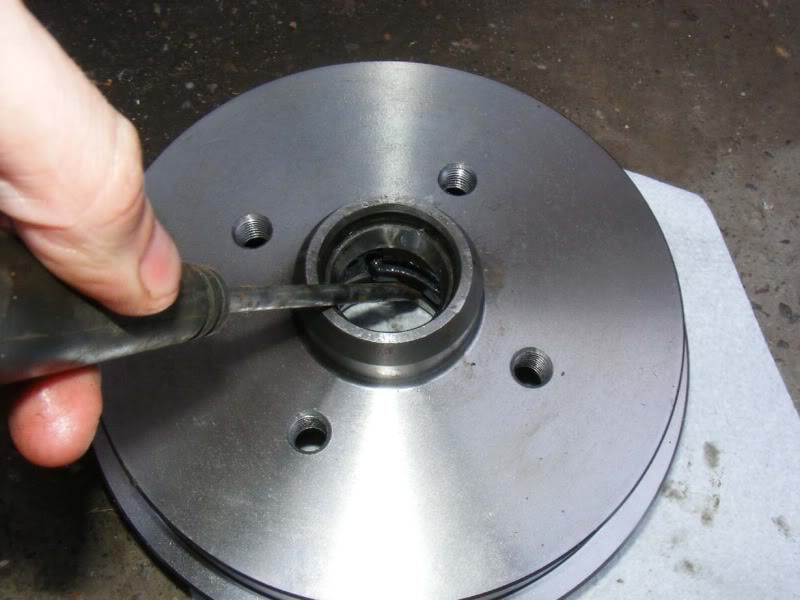
Step 113 - Now when it comes to the bigger bearings, I think you will really struggle with the chilling alone so now we need to use another tip, baking! Put the hub in the oven on gas mark 2 for 20 minutes, it will be plenty hot enough after that
Try not to leave oil in your oven, it's not good for you - especially if you have a wife who likes the oven! A baking tray etc will catch any lubricant that seeps out of the hub
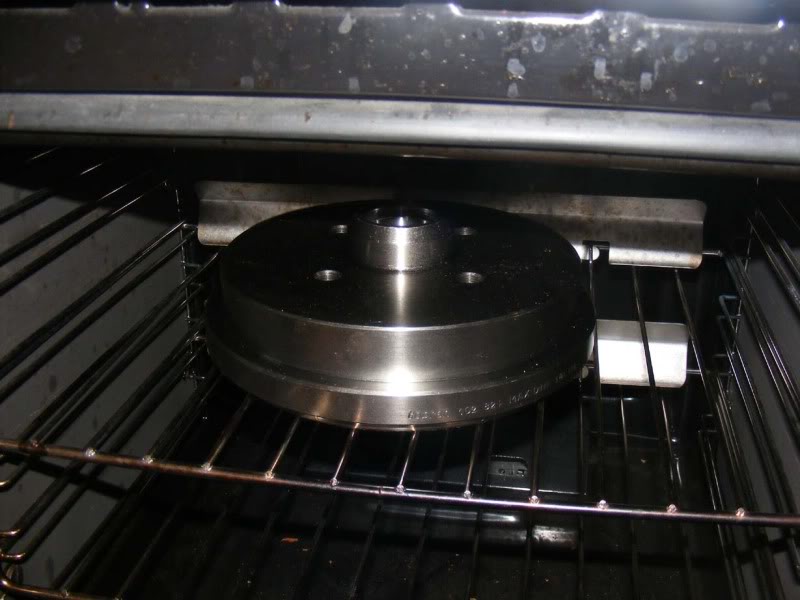
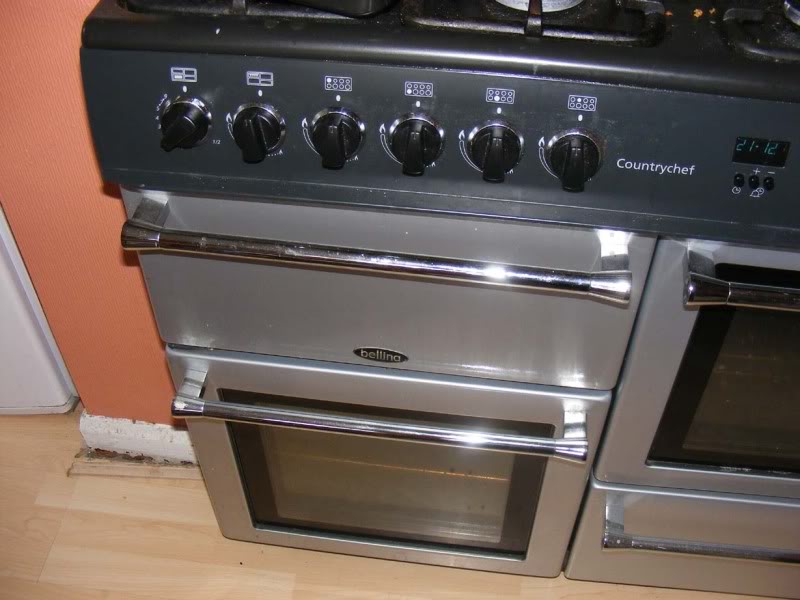
Step 114 - Take your steaming hub out with an oven glove and go back to your working area
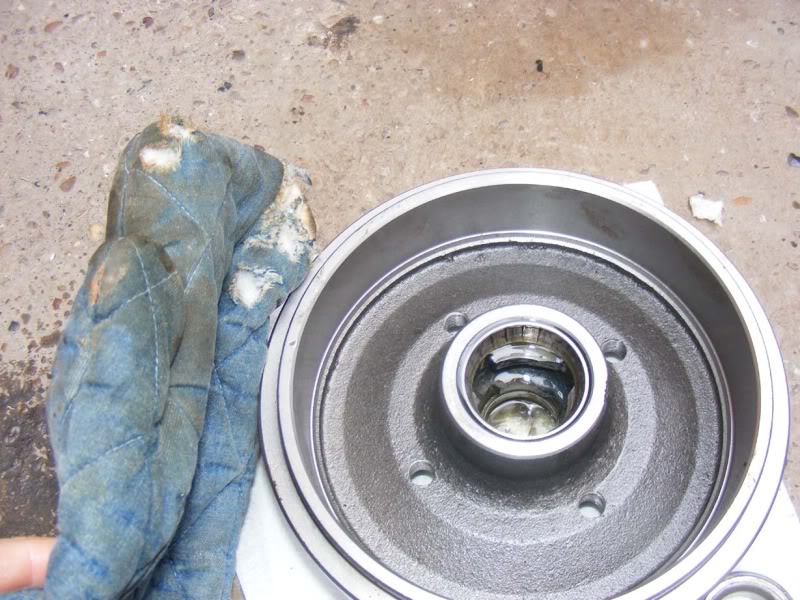
0 guests and 0 members have just viewed this: None.