new member mad idea ,mk1 caddy 4motion 4wd turbo 24v......
Posted
Settled In

new member mad idea ,mk1 caddy 4motion 4wd turbo 24v......
how cold wa it this after ,,thought chuff it lol
managed to do a bit more on the rear bad pic but its a inch lower lol ,but im now thinking wheather to thow some 18s on it ,,what do u think..
ill have to fit the head spacer/gasket and some nice copper sealer too
add to sort the ecu as the buggar needed 3 spark outputs and nice lauch control lol
managed to do a bit more on the rear bad pic but its a inch lower lol ,but im now thinking wheather to thow some 18s on it ,,what do u think..

ill have to fit the head spacer/gasket and some nice copper sealer too

add to sort the ecu as the buggar needed 3 spark outputs and nice lauch control lol

Posted
Local Hero

yay megasquirt you the man

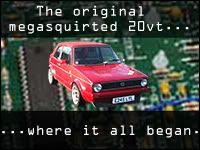
Posted
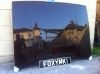
Local Hero


adaptorman said
just picked up a nice high flow red band holly feul pump,this may do the joby,,,
![]()
that looks familiar,
Posted
Settled In

has to be easyer then messing with crapy mk4 wireing loom ,plus is lappy mapable ,,adds to the hmemade way lolbens_cab said
yay megasquirt you the man![]()
Posted
Settled In

really?got rid wasnt good enoegh got this instead.. it will run 4bar all day ,unlike the otherfoxymk1 said
adaptorman said
just picked up a nice high flow red band holly feul pump,this may do the joby,,,
![]()
that looks familiar,

Posted
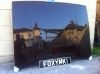
Local Hero


last time i saw that was in joes garage, he said your abit mad lol lol
keep up the good work pal, il pop up to mexbrough next time im in donny pal joe said me and you need to meet :mrgreen:
keep up the good work pal, il pop up to mexbrough next time im in donny pal joe said me and you need to meet :mrgreen:
Posted
Settled In

tidy i thought ,this guy must know joe lol ,,he says im a bit nutty ,hes worse then me lmao ,hes just scared of welding petrol tanks …………..im not ,,,lolfoxymk1 said
last time i saw that was in joes garage, he said your abit mad lol lol
keep up the good work pal, il pop up to mexbrough next time im in donny pal joe said me and you need to meet :mrgreen:
Posted
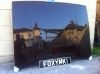
Local Hero


Posted
Local Hero

i welded an old bedford cf fuel tank once i was well prepared tho washed it out then lowered the bedford on the ramp onto the petrol tank so it didnt go anywhere then sporting a leather bike jacket and acrsh helmet proceeded to weld it dont what people are worried about tbh :mrgreen:
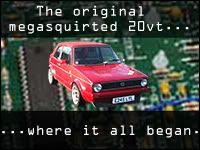
Posted
Settling In

apparently if you hook a petrol tank up to the exhaust of a running car and fill it then its safe to weld.
i however am not brave enough to try it!
i however am not brave enough to try it!
Posted
Settled In

lol yes i agree he cant evern hold pliers ,lmao little videofoxymk1 said
lol, hes gettin old, lol
http://tinypic.com/player.php?v=1z3ue7p&s=4
Posted
Settled In

lol cool ,we weld with feul in them lmao ,its more fun ,least keeps u warm on these winter days ….bens_cab said
i welded an old bedford cf fuel tank once i was well prepared tho washed it out then lowered the bedford on the ramp onto the petrol tank so it didnt go anywhere then sporting a leather bike jacket and acrsh helmet proceeded to weld it dont what people are worried about tbh :mrgreen:

Posted
Settled In

havent tryed this ,but if the cars on a cold start then ud have overfeul from the exhaust pipe ,,i reckon theres would be a nice fir on the go… 8Ojohns-jetta said
apparently if you hook a petrol tank up to the exhaust of a running car and fill it then its safe to weld.
i however am not brave enough to try it!
Posted
Settled In

small update
only had a hour free,this isnt the best of pic ,but it the inner side off the pedle as this bit of weld usely breaks from factory ,so beefed it up ,,saves having to buy a new slave at 120/vat lol
then quickly drillede and bolted in place
hit a small prob on the bulk head ,,nothing major ,so nipped a bit out ,as i wanted the hydrolic pipe in the rail,,
job done ill sort a fluid bottle later …
just warmed the bendy steel pipe ,and bent it straight,,,you can just see,
only had a hour free,this isnt the best of pic ,but it the inner side off the pedle as this bit of weld usely breaks from factory ,so beefed it up ,,saves having to buy a new slave at 120/vat lol

then quickly drillede and bolted in place

hit a small prob on the bulk head ,,nothing major ,so nipped a bit out ,as i wanted the hydrolic pipe in the rail,,

job done ill sort a fluid bottle later …

just warmed the bendy steel pipe ,and bent it straight,,,you can just see,
Posted
Old Timer

You certainly live up to your name! 8) good work looks awesome!
Posted
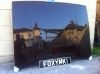
Local Hero


adaptorman said
lol yes i agree he cant evern hold pliers ,lmao little videofoxymk1 said
lol, hes gettin old, lol
http://tinypic.com/player.php?v=1z3ue7p&s=4
lol
Posted
Settled In

i wasnt happy with the rear arm as it was catching the dam spring and hitting the subframe so decided to alter it ,,this sorted the buggar out
fits and clears better
then start on the shorting the drive ,as i thought this may help incase anyone wants to try it ,
first cut the drive shaft to size and make it in to a pencil point
then once grind out ready place both halfs flat agaist the angle iron ,and mig tac to hold it in place ,then just give the centre a quick weld in the centre ,
once thats in place ,u really need a stick welder ,ive a 150amp one useing 2.5 rods ideal for drive shaft welding
fits and clears better


then start on the shorting the drive ,as i thought this may help incase anyone wants to try it ,
first cut the drive shaft to size and make it in to a pencil point


then once grind out ready place both halfs flat agaist the angle iron ,and mig tac to hold it in place ,then just give the centre a quick weld in the centre ,


once thats in place ,u really need a stick welder ,ive a 150amp one useing 2.5 rods ideal for drive shaft welding
Posted
Settled In

right a little bit done this after , ,but dam rain ended it ,
so first it was time to start filling the drive shaft with stick weld ,lol
then grind it up,no sleve required
thats what i call spot on ,,,,so lets see how true my idea with angle iron
too short videos,,
first the angle test
View My Video
then on the car
View My Video
next thought due to getting a nice shock of the welder lol
thought ,
so first it was time to start filling the drive shaft with stick weld ,lol

then grind it up,no sleve required



thats what i call spot on ,,,,so lets see how true my idea with angle iron
too short videos,,
first the angle test
View My Video
then on the car
View My Video
next thought due to getting a nice shock of the welder lol
thought ,
Posted
Settled In

chuff the welding due it raining all day
so thought ill sort the clyinder head out
rocker removed
head removed and cleaned etc
checked all bores etc and cleaned plus decoked pistons ,
some nice copper spray to seal everything on the block
then split the std 3 layer gasket use the down part first
then another coat of spray and fit the head spacer to lower compression
another quick coat of spray fit the top part of the gasket as the middles not used and bingo job done ,
and did a final check of the timing as i dont want valve nicely wacking pistons etc lol
final pic of the head spacer ,somert else out of the way lol
so thought ill sort the clyinder head out
rocker removed

head removed and cleaned etc

checked all bores etc and cleaned plus decoked pistons ,

some nice copper spray to seal everything on the block

then split the std 3 layer gasket use the down part first

then another coat of spray and fit the head spacer to lower compression


another quick coat of spray fit the top part of the gasket as the middles not used and bingo job done ,
and did a final check of the timing as i dont want valve nicely wacking pistons etc lol

final pic of the head spacer ,somert else out of the way lol

Posted
Settled In

mate that welding on the shaft is a work of art ? i take my hat of to you my frend ,lovin the build ?
There are too many online users to list.