Great - Water in cylinder head!
Posted
#1640947
(In Topic #228777)

Newbie

Short story :
Was running fine a few years ago until a core plug burst and he ran it hot. New Core-plugs fitted all round, had old cyl head refurbed at local shop .Fitted it,started up,water gushing out of air box like a fountain. Can't go back to engineers as gap between refurb and fitment was a very long time.
Complete engine strip down, purchased 2nd hand head - told it was good-(yep I know we took the risk) torqued down correctly, new H/G, filled engine with oil and water in coolant-left alone for few weeks while life got in the way.
Came back to it other day and tried to fire it up on starter but no chance as we'd not set the timing correctly. Lots of turning at the crankshaft bolt end to get TDC and then we found it became increasingly harder to turn over by hand and starter motor was struggling. knew immediately something very bad wrong….thought hydrostatic lock etc.
Drained sump and yep,water came out,complete strip down ,everything oiled up waiting for the cyl head to come back from engineers who have now pressure tested it and they said it was holding ok but in their words they said it was banana shaped so i take that as warped.
Okay,so we've just had cylinder head back,got a new h/g, and getting ready to try again.
Question - But could it be something other than the cyl head that is causing our problem?
How about the bottom end? it's his original but could there be a failure in either the water jacket in that or something? or how about the oil cooler,which the oil filter screws onto,could we have pipes routed incorrectly there or a hole inside causing oil and water to mix?
I am willing to change the bottom end to another,and purchase another oil cooler if it saves us repeating this.
any advice or tips much appreciated.
Please see the cyl head after i took it off,it was all ky jelly like in there.
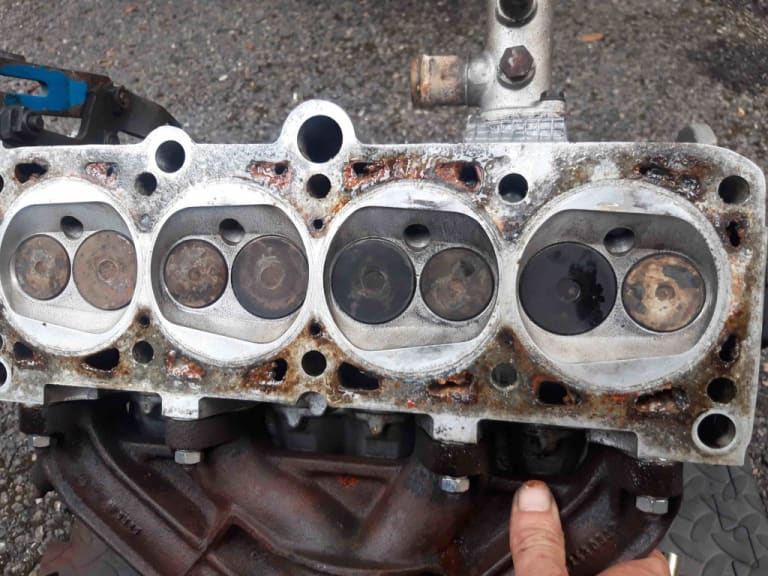
Posted
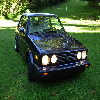
Local Hero

I would clean the mating surfaces of that head to clean out the ports and gully's You are using new bolts, as you can't re-use bolts. It doesn't take much to cause a head gasket to fail as far as crud on the mating surfaces go,,, and that is a lot of rust inside the galley's
So I would suggest that it needs a good cleaning as well.
Banana shaped, need a better description, Cylinders oval out usually and need to be bored true. Banana shape tells me that they are close at the top different at the bottom and middle…
Which cylinder filled with water? and the reason why water gushed out of the air box, (CIS dosen't like water……)
because a Cylinder was pushing it out….. Your head can be cracked internally….if they found no cracks in the cylinder walls.
I would suggest a new Oil Cooler they aren't that costly you can have your checked or do it yourself using a couple of rubber bungs and putting air in it while it is submerged in water…see if it bubbles…..
What do Divorces, Great Coffee, and Car Electrics all have in common?
They all start with GOOD Grounds.
Where are my DIY Links?
They all start with GOOD Grounds.
Where are my DIY Links?
Posted
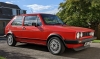
Old Timer


To get water coming out the airbox can only mean it was coming back through the inlet valves so the timing can't have been right on that.
If the head has is good, then as you have suggested, the water jacket in the block could be compromised - not sure how you can test for that. If it has been run hot there may well be a crack. Although, under normal circumstances if there was a leak between the water jacket and the cylinder the pressure in the cylinder would normally push the air back into the water under the compression stroke. If you can blank off the water pump housing, you could put water in the block (with the head off) and see if you can see any leaking into the cylinders.
If the leak was in the oil cooler, you wouldn't get water in the cylinder as you don't have oil in the cylinder.
Did you have the cylinder head skimmed?
Sounds like a new bottom end to me.
Posted
Newbie

I'm willing to bet now you have a freshgly skimmed head and a new gasket that you be all ok, definately worth a coolant system pressure test after assembly, just use plain old water until you know its ok and chuck in a flush and drain to get rid of the crud in there.
Best of luck.
Posted
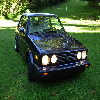
Local Hero

Do not re-use bolts.. they are 1 use only, and if you are thinking about taking them off in the Future, I strongly suggest the ARP racing stud kits as they are re-usable.
I have always hated that X Nm/Ft/lbs then 1/2 turn….gimme a definitive torque…..
What do Divorces, Great Coffee, and Car Electrics all have in common?
They all start with GOOD Grounds.
Where are my DIY Links?
They all start with GOOD Grounds.
Where are my DIY Links?
Posted

Newbie

On balance I do think our water problems were probably due to not getting the head skimmed! - mental note made.
I have remembered that when I torqued it down last time..the two Haynes manuals I'm referring to when doing work on this engine …had conflicting torque settings so we settled on a figure in the middle and then turned it another so many degrees like the manual says but can anyone clarify what the exact torque setting is for the head bolts? Perhaps I also didn't torque it down enough?
I do remember doing a compression test on the engine cyl's and they all recorded similar and and within spec range.
Anyway, the skimmed Cyl head is back and only negative thing I can see is a corner of a hole where the aluminium has gone flaky ..should i be concerned? There still looks to be plenty of meat there (Attached picture)
I've also attached pics of the top of the bottom which we are going to clean up once we mount it in an engine stand.
Re: pressure testing - This might be a good idea to check but I have never done this and I'm not sure what I'm looking for when buying a suitable kit to test for this so can anyone steer me to the right kit?
I want to add a small but might be significant detail …..that when my friend bought this car the seller told him it had had £££ spent on it and for a few years it ran perfect and pulled like the clappers. After my friend ran it dry after the core plug failed, we stripped it down we found that it had indeed been over-bored by half a mil with oversized pistons and rings. We are still using the original bottom end obviously but with new core plugs fitted.
Posted

Newbie

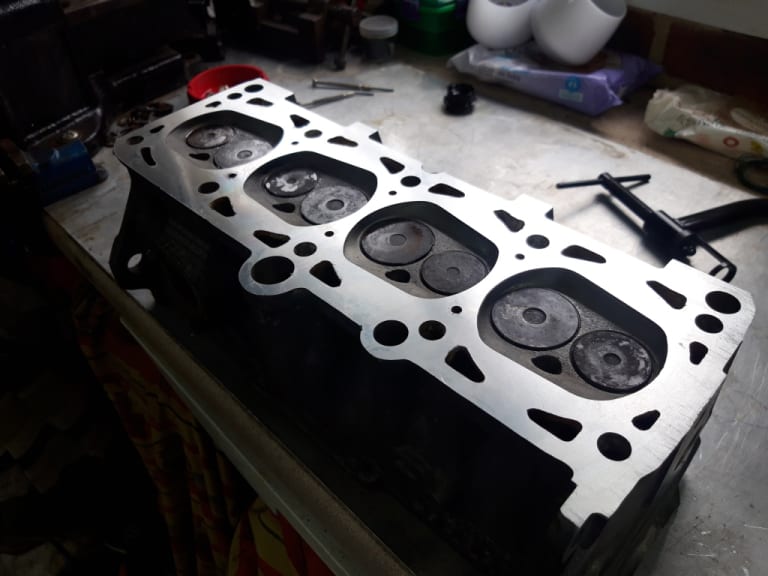
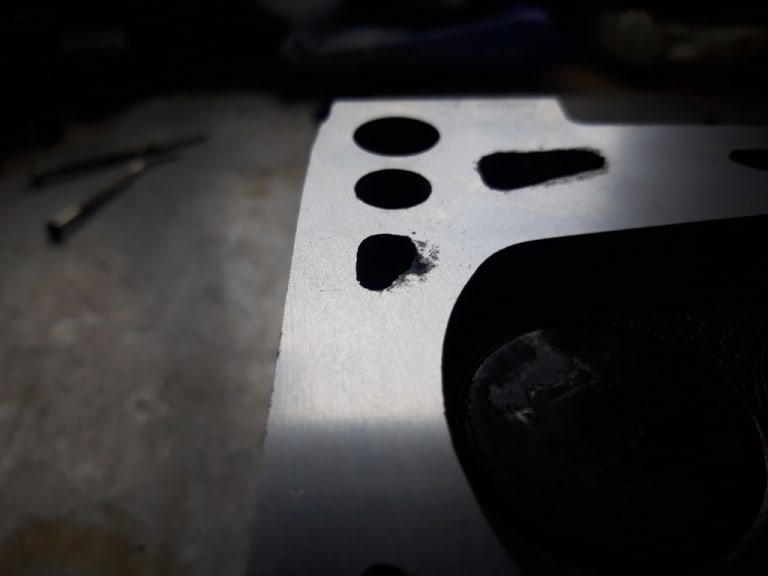
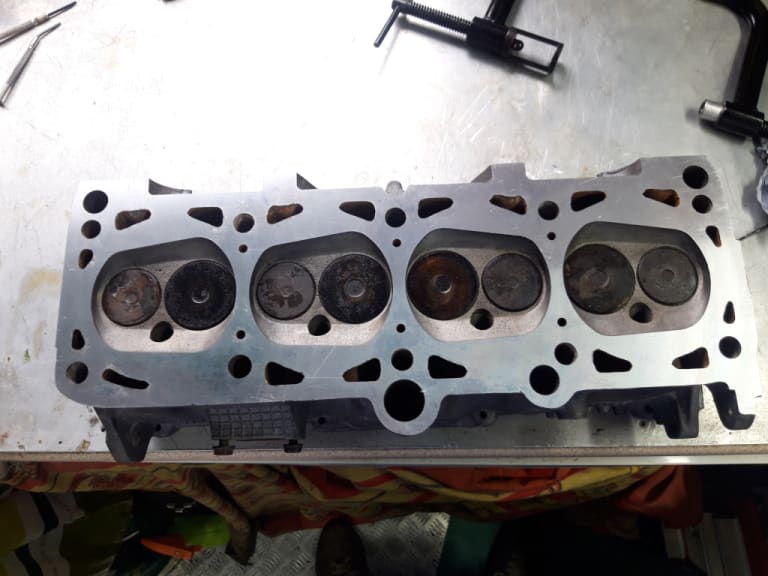
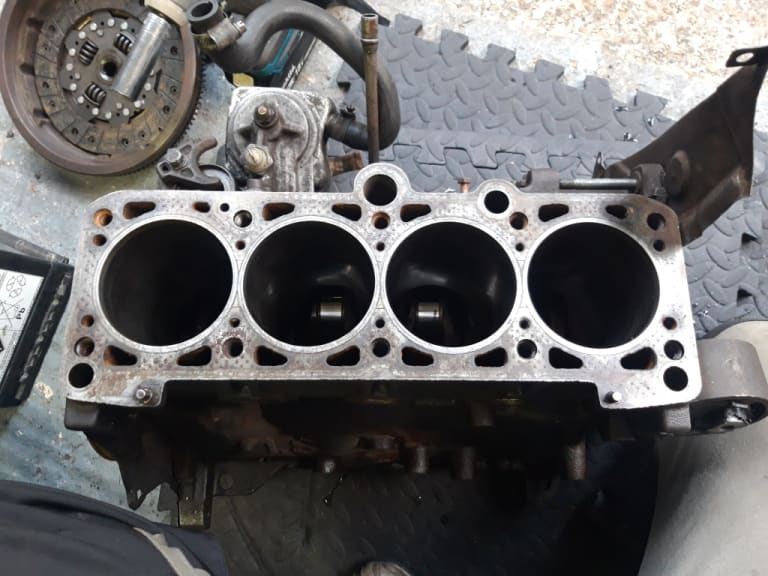
Posted
Local Hero

You have a head which was warped? Is the block warped too? Did you check its top surface for flatness? Because fitting a flat head to a warped block won't seal properly.
Now that you have a decent head, its a good chance to check the block properly, de-coke it a bit if you want, and refit everything. Also replace the oil cooler (its cheap, everything is in bits, and eliminates an issue).
There will still be water in the oil and oil in the water, so if/when its actually running, these will need a good flushing out. Its one of the few instances its probably worth doing an engine oil flush. Coolant….there's products you can add to flush it out decently I think? And/or you can take a few hoses off and get a decent flow of water from a hosepipe, let it run for a while.
Only once you have a new head on a flat block, with the oil and coolant flushed out, you can diagnose any further issues.
Posted
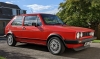
Old Timer


I'd suggest that the leaky core plug and hot running warped the head, and that is the cause of your problems. I wouldn't worry about the bit of corrosion on that water way in the head - the gasket will deal with that.
Regarding torque - if it's a 1.8 DX engine then the correct values are in the Supplement - Section 12 - of the brown Haynes manual.
If it's had work done on the bottom end, that's a bonus! Sounds similar to mine - slight over bore and new pistons and rings.Can't image they wouldn't have done the shells at the same time, so should be sound.
Posted
Newbie

sparkybandit said
Thanks to all for the advice! It's felt like one step forward and two steps back sometimes on this car but like I say to my mate Have we ever done this before? Nope. so what do you expect. I'm positive that with an optimistic outlook and some community help we can get this motor running sweet again.
On balance I do think our water problems were probably due to not getting the head skimmed! - mental note made.
I have remembered that when I torqued it down last time..the two Haynes manuals I'm referring to when doing work on this engine …had conflicting torque settings so we settled on a figure in the middle and then turned it another so many degrees like the manual says but can anyone clarify what the exact torque setting is for the head bolts? Perhaps I also didn't torque it down enough?
I do remember doing a compression test on the engine cyl's and they all recorded similar and and within spec range.
Anyway, the skimmed Cyl head is back and only negative thing I can see is a corner of a hole where the aluminium has gone flaky ..should i be concerned? There still looks to be plenty of meat there (Attached picture)
I've also attached pics of the top of the bottom which we are going to clean up once we mount it in an engine stand.
Re: pressure testing - This might be a good idea to check but I have never done this and I'm not sure what I'm looking for when buying a suitable kit to test for this so can anyone steer me to the right kit?
I want to add a small but might be significant detail …..that when my friend bought this car the seller told him it had had £££ spent on it and for a few years it ran perfect and pulled like the clappers. After my friend ran it dry after the core plug failed, we stripped it down we found that it had indeed been over-bored by half a mil with oversized pistons and rings. We are still using the original bottom end obviously but with new core plugs fitted.
As Paceman said dont worry about the flaky bits, from the pics that head looks a thousand times better than before. Get yourself some wet/dry medium grit sandpaper and a sanding block and go over to block face, doesn't have to look perfect just smooth and free from old gasket and surface corrosion.
Regarding a pressure tester it would be better to borrow one or get your local garage to do it as its expensive just for one use., but up to you and your budget.
If you need any specific torques let me know as i have access to AD and will have a look for you.

Posted
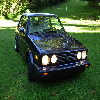
Local Hero

The Official ARP Web Site | Kits
Read the instructions set torque to 80 ft/lbs none of this 1/2 turn garbage……
I had wished I new about them when my Diesel had to have the head removed for a blown gasket, and that little sucker never failed to blow a gasket about once a year for the last 5 or 6 years I owned it (prior to the interweb)…the only nice thing is that I learned how to remove and replace the head gasket in a diesel in about 3 hours start to finish…

I also learned that if I removed the exhaust studs and replaced them with Stainless Steel ones that had the hex driver ends to make seating them a joy, that with the things slathered in Copper Grease as you call it (I use the term never-seize) it was never a pain in the keister to remove them or the nuts that held the manifold on….
Oh, and removing them on the car or off the engine use penetrant on them for 3 to 5 days prior a 6pt socket 12mm and a air or electric low profile Impact tool you won't shear them off.
m8X30
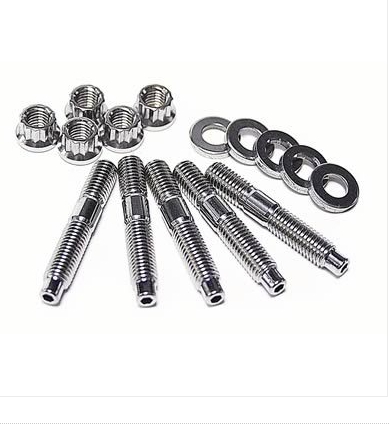
https://www.napaonline.com/en/p/NDP81952201?partTypeName=Exhaust+Manifold+Stud+and+Nut+Kit&keywordInput=exhaust+manifold+studs
Trust me when I say that removing a head with both manifolds attached is a right royal pain.
What do Divorces, Great Coffee, and Car Electrics all have in common?
They all start with GOOD Grounds.
Where are my DIY Links?
They all start with GOOD Grounds.
Where are my DIY Links?
0 guests and 0 members have just viewed this: None.